Master-Feeder-System MFS-V3
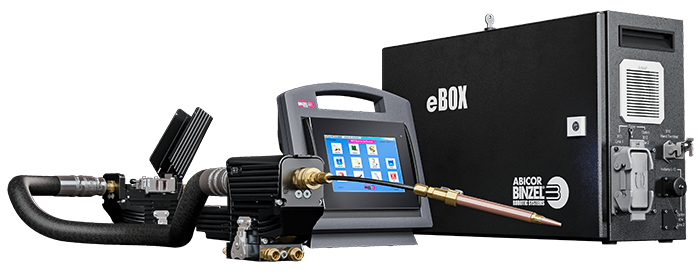
Precise Laser Wire Feeding
The MFS-V3 wire feeder system (third generation master-feeder system) features a reimagined eBOX. With its modern and precisely matched components, the eBOX is made special for the laser brazing demands of vehicle makers around the world. Compatible with MFS-V2.
MFS-V3 Features & Benefits:
- Digital wire feeding system with fast and precise control for high-precision laser applications
- Two controlled drives for high-dynamic operations
- Wire buffer function for virtually frictionless wire feeding and low maintenance
- Usable with an in-process drive as a master pull system for short to medium distances
- Wide-range input for different supply voltages globally
- Analogue, digital or field bus activation for direct and job operation
- Extensive service software with visualization and documentation
- Simple update via SD card slot with user-level release possible using key stick (USB)
- Optimization of the load transmission to the wire by adjusting the spring tension
- Simplified installation and dismantling of the wire feed rollers
- A new pressure system at the wire sensor prevents the incorrect setting
- Ceramic wear parts available for high-temperature requirements
Master-Feeder-System V3 Components at a Glance:
Manuals
Document language
eBox V3 Control Box

The third generation of the master-feeder-system features a comprehensive new development of the eBOX control unit that is used to meet the complex requirements of wire feeding in laser applications. The result is a completely reworked and optimized eBOX with modular and precisely coordinated components. As the nerve center of the system, it is ideally equipped for the ever-increasing requirement profile in laser applications – particularly in car manufacturing – all over the world.
The eBOX represents the communication interface between the higher-level plant control and the wire drives of the MFS-V3. It houses all the electronic control elements and is available as an analog/digital version and digitally for various Fieldbus systems/interfaces.
Fully digital control circuits as well as the consistent separation of logic (Multibus I/O board) and drive technology (axis controller) ensure that individual system components are reproducible in the case of servicing and are replaceable without further adaptation. Time-consuming calibration of analog tachometer systems or other components, therefore, belongs to the past: fully digital control for a futureproof system.


MFS Service Software - For Complete Control

MFS service software is the comprehensive software package for management, diagnostics, operating status display, fault evaluation and quality recording.
For the third version of the MFS, the tried and tested service software has been completely reworked, improved and extended with many additional functions.
As usual, the software – which is now licence-free as standard – can be used with the existing system PC in conjunction with an eBOX. As an alternative for managing several eBOX devices, the innovative MF-Control operating panel with fine and precise touchscreen is now also available, making operator work easier.
The simple and intuitive software user interface allows straightforward use of all functions. For safety, users can be given different usage rights. This is done by assigning a user level. Users identify themselves and log in with a user login and password or alternatively with a key.
Service Software Features & Benefits:
- Setting and editing of up to 64 different jobs
- Comprehensible documentation of the processes
- Fault display in plain text
- Fault log with analysis and troubleshooting
- Creation and management of freely definable maintenance intervals possible
- Diagnostics: clear system status display, which shows directly whether the system is operational or whether there is a fault
- Several eBOX devices can be given station information by assigning the IP address
- Saved station information is shown in the log files
- Multilingual user interface: six different languages can be selected (English, Spanish, French, German, Italian, and Polish)
- Setting the wire buffer function
- Three user levels:
• 0 (read authorization)
• 1 (authorized to load the config. files)
• 2 (administrator rights)
Flex Supply - Wire Feeding Close to the Action

The Flex supply provides superior feeding of the wire into the process and works as the interface between the wire feeding system and the workpiece. It is fixed to the laser optic and adjusts exactly to its movements.
The Flex supply acts as the securing nut fitted on the MF3 drive and the feeding body with wire feeding nozzle. The connection between the two components is made by a flexible liner. Depending on the wire diameter and material, various liners and wire feeding nozzles can be utilized.
The feeding body is available both for cold and for hot wire feeding applications. The cold wire variant comes with or without gas feed. The hot wire version is available with gas feeding and cooling; the gas and the coolant are fed separately to the feeding body.
Flex Supply Features & Benefits:
- Can be shortened individually due to the flexible liner between feeding body and securing nut
- Feeding body for cold & hot wire with or without process gas
- Can be adapted to all standard laser optics
- Quick, safe fitting and changing of the body with a specially adjustable clip system
- Excellent accessibility and optimal seam surfaces due to new design with coaxial gas feed
- With the new design, the gas nozzle is no longer required, which reduces the wear parts
MF3 Front Drive - The Driving Force
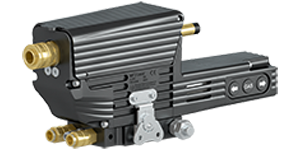
The robust and powerful MF3 front drive brings the Master-Feeder-System to life. Developed specifically for laser applications, MF3 excels in performance with its small size, low weight, and variety of connection systems. It can be used individually or in conjunction with the rear drives (master pull or dual push-push system).
The centerpiece of the MF3 is the 4-roller drive in combination with the fast, digital motor control via the new eBOX. The 4-roller action guarantees minimum slippage and prevents wire deformation from pressure force. The short acceleration and response times, vital metrics for laser applications, are easily attainable.
The drive/specification speed is monitored and controlled by a built-in encoder. Actual wire speed is determined with the aid of the actual value transmitter for the wire and forwarded to the service software. The easy accessibility and the quality of the wearing parts allow quick and simple replacement of wearing parts and reduce downtimes.
MF3 Front Drive Features & Benefits:
- 4-roller drive
- Small size and lightweight
- Monitoring of feeding speed by actual value transmitter (AVT) for the wire and service software
- Reworked pressure rocker for adaptation to increasing service requirements
MasterLiner - Smooth Wire Flow
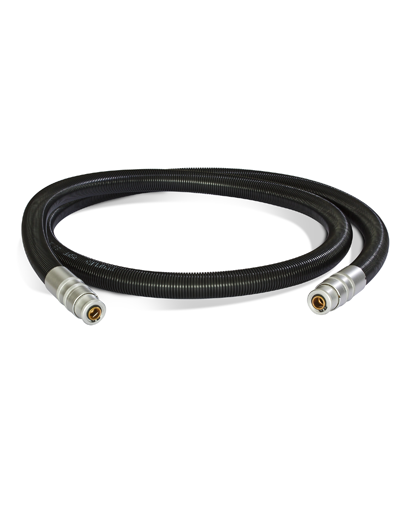
MasterLiner sets a new standard in wire feeding. They consist of individual segments, each of which can be rotated by 360°. Four small rollers in each segment ensure smooth wire feeding with virtually no resistance.
The MasterLiner system is available in the MasterLiner and the MasterLiner MAXI designs, in HD and FLEX versions. The flexible FLEX version – consisting of a corrugated tube and variable connection system – allows for easy, free assembly of the desired length as well as problem-free repair directly on site, saving time and money.
The heavy-duty HD variant is sheathed in a resistant aramid fiber reinforced protective fabric and has been developed for extreme applications.
With the use of the roller-guided MasterLiner changing electrodes is no longer needed, meaning time-consuming maintenance work on the cable assembly no longer applies.
MasterLiner Features & Benefits:
- Low friction force
- Long durability
- Cleanable by ultrasonic bath
- Maintenance-free and low susceptibility to faults
- Wire feeding possible over long distances and with a single drive
- Suitable for all wire types
- Easy, quick setup and replacement due to quick-release
Rear Drives – Additional Power if Required
For certain applications, it is recommended to operate the MFS-V3 system with a second drive as a dual push-push system to guarantee reliable processing of the wire feeding.
One criterion in the decision is the length and condition of the wire feeding route. For long distances or complex routes affecting the liner management, a rear drive is needed to guarantee an even feed. Material properties are also significant. Soft wires such as aluminum require two drives to prevent any tensile forces acting upon the wire so the wire is pushed evenly and not pulled undesirably over the length.
With the additional drive, the forces acting on the individual components in the system are minimized and the wear reduced. The two drives are each addressed separately by the eBOX via their own control circuit to keep response times as low as possible. Synchronization between the drives is not necessary.
The wire buffer function of the system is new and controlled by the intake current of the rear drive. This ensures that the MasterLiner is refilled with enough wire after each cycle. This function guarantees better wire feeding performance, particularly at the start.
MF3 Rear

Structurally identical to the MF3 front drive, the MF3 Rear includes the positive characteristics of it's big brother.
The two are distinguished only by the actual value transmitter for the wire (AVT), which is not required in the MF3 Rear.
The identical wear parts system makes it the perfect addition to the main drive and lowers part costs.