MIG Gun Maintenance Guide
Let’s start with who this guide is for and why you would use it. Your MIG welding guns are vital pieces of equipment and are relied upon daily to keep your weld production running smooth. But, welding guns are often subjected to misuse from welders who are not familiar with how to properly care for them.
This guide will teach Supervisors, Production Managers, and Welders how to maintain their welding guns so these pieces of equipment last as long as they should. Whether you or your company has a new group of welders, have created a new department, or going through your
welding guns faster than you believe you should, this guide will help you identify areas of focus. It will also guide your preventative maintenance (PM) program to ensure your equipment returns more value and you produce more parts faster and for less.
Want the Printer Friendly PDF? Click the Button Below to Download:
About the Author
Dave Detmer is District Sales Manager for ABICOR BINZEL USA in the Midwest Region. Dave has nearly 15 years of welding experience beginning with his time in the U.S. Marine Corps.
Dave has worked as a pipe welder, weld technician, lead fitter, and currently works in district sales. He has held numerous maintenance trainings for MIG torches and robotics to assist manufacturers in maximizing the value of their welding equipment investment.
Dave can be reached at ddetmer@abicorusa.com .

"My typical process when I do MIG Gun maintenance is to tailor it to the customer. This can be as detailed as breaking a gun completely down to all the parts and pieces. The common preventative maintenance and inspection tasks you run into will be around what you see in the Table of Contents.
This guide will cover wear signs, best practices, places to check, and preventative maintenance for each of these."
Let’s start with welding contact tips. As the part of your welding gun that is responsible for both guiding wire and feeding current, it’s the most worn item for any welding gun. The contact tip is the forefront of the weld gun.
Whether you’re dealing with a manual welding or your robot welding, the purpose is the same for each respective torch.
Your contact tip is also a constant wear item. No matter the type of wire you use or gas mix you weld with, the tip will wear and need replacement. Some wires wear tips differently than others, but in time they are all wear.
Sign of Contact Tips Wear
It is a common practice for welders and production teams to discard contact tips prematurely. Largely this has to do with a lack of knowledge on how to identify a worn contact tip. Seeing the tip blackened or spattered, for some are signs of replacement.
Other times it’s habit. Welders change out contact tips after a break period or a certain number of parts in the habit of ensuring they have a fresh part.
These are not the signs or reasons to determine whether the part needs replacement.
The first and most telling sign of contact tip wear is going to be the orifice of the tip no longer being round. Usually that contact tip orifice will be egg-shaped or oval-shaped, from the cast of the wire wearing on one side of the tip versus the other.
This constant motion of moving wire at higher temperatures wear the orifice and elongates it, affecting wire feed and current transfer.
Wire whip, or wire wandering, is the first issue you encounter with a worn contact tip. This causes the wire to go where not directed. It floats inside the contact tip and can affect the location of the weld.
In robotics, this is a much more pressing problem. In manual welding, the operator can manipulate the gun to direct that wire into the weld puddle provided they notice. In robotic applications, when the wire starts to move around, it will cause issues in and about the joint.
Worn contact tips will immediately result in lost current transfer. Loss of current causes arcing inside the tip, especially as it gets more worn, or it can cause burnbacks. Burnbacks are when the wire arcs inside the contact tip instead of the weld piece, which can fuse the wire to the inside of the tip.

When you encounter burnbacks, first thing you do is check tip life or tip wear, and make sure the size of the contact tip is right for the wire being used. You can look at tip wear similarly with an oversized tip. If you are running a 1/16” (.062) tip for an .045 wire, it might be feeding wire without obvious issues, but it will cause internal arcing issues inside of the tip and a consistent amount of burnbacks.
Using Oversized Contact Tips
A common cause of premature wear on contact tips that I encounter is using oversized contact tips.
This is a common scenario: A station uses two different sized wires to weld a part. A normal instance is the production line use .035 wire and 1/16” wire. That is a sizable difference in contact tip size. Many companies try to reduce inventory or make it less confusing by using the larger contact tip size across the entire line to feed and weld with both the .035 and 1/16” wire.
That will work to get the job done, but it ensures you will prematurely wear your larger size contact tips. Anytime you run an undersized wire through an oversize contact tip it will have limited current transfer, consistent micro-arcing of the contact tip, and be the contributing factor to premature contact tip wear.
Most welding operators use this practice to cut corners. It means for them one less part of stock, but it's a detriment to production. Overall, doing this increases downtime and increases part spend.
Check your production line to confirm you are using the correct contact tip size in relation to the size of the wire. Running an oversized tip for the wire is a practice to avoid.
A high quality contact tip, whether copper tip or copper alloy, should get several pounds or multiple rolls of wire welded on one tip. If you are not getting that result, investigate why to ensure it’s not a bad practice contributing to the problem.

Undamaged contact tip (left) vs damaged contact tip (right)
Premature Contact Tip Change-out
A poor habit I also see is a premature tip change. Usually this is a matter bad habit. Welders will change out a tip at every break or after every fifth part or something arbitrary in the habit of making sure they have fresh parts.
In some case it's needed. You might get an abrasive wire and it's going through tips quicker than it does with other wires.
Or, it might be you have dirty wire, dirty material, and it's causing some burnbacks, spatter adhesion, or process related issues.
Those types of challenges will definitely wear your contact tips faster.
Generally, however, it’s more important to look for a physical sign of wear than simply anticipating the part being bad.
That tends to be a drain on time, productivity, and consumable spend.
Contact Tip Not Threaded Tight
Another common practice that I typically see is contact tips not tightly threaded. Strictly hand-tightening contact tips will cause issues with current transfer and high resistance, which effects the temperature of the tip, which prematurely wears the part.
The clearest physical sign of a loosely tightened contact tip on the tip holder or diffuser is the thread of the tip being discolored.
The threads of the type will be a purple-blue color, similar to a part that is thermally hot. That discoloration is a sign of excess heat in the contact tip. Loose connections break down the copper and wear through the tip much faster than a properly threaded part.

This practice goes hand in hand with prematurely changing out contact tips. Welders can get in the habit of changing tips out frequently because they want to change them out quickly. When that happens, they hand-tighten them instead of using their tools.
A practice like that undermines prioritizing speed in a contact tip change. Since those contact tips aren't tight, they get poor current transfer and high resistance and wear it out faster than they should.
Contact tips thread for a reason. You know when they're tight and you know when they're loose. There is no in between about it.
The best practice is to tighten it by hand and then just snug it up with a tip wrench after. What you want more than anything from that tight contact tip connection is for that current transfer to go through the shoulder of the tip.
You want the majority of that weld current to go from the thread through the tip base. Otherwise, the threads will get excess heat from carrying too much current.
Filing Contact Tips
Contact tips are precision machined. They either are drilled-through or at minimum extruded with a mandrel.
The idea that tools such as round files can smoothen the internal diameter or internal orifice won’t have the desired effect you’re hoping for. It is a practice I have encountered and is not one I recommend – especially using higher quality, machined contact tips.
Yes, the tips looks smooth after some time, but it's not near as smooth as what they come from the factory after being drilled or machined. This practice creates a negative effect by running the file inside of that orifice, making the inner bore uneven, and creating more issues than solving with the contact tip.
Anti-spatters and Chemicals
The best ways to increase your contact tip life is make sure your wire feed's set properly, you have proper drive roll tension (most are too tight), proper liner size, the proper tip size for the wire you're using, and avoiding too many oils, like anti-spatter being on the tip.
If you use anti-spatter such as ceramic spray or nozzle gel, less is more.
Many anti-spatters are silicone-based or wax based. This causes issues with the contact tip. Wax or the silicone-based chemical break down and create a residue.
This residue then starts to collect and trap dust and other debris. This means spatter and other things like that become more prone to sticking at the nozzle and wearing down your contact tip.

Comparing Good and Bad Contact Tips
A good tip will have an orifice that is round and looks clean on the front end. The threads aren't annealed or discolored. The tip provides good current transfer from the internal parts of the gun to the wire.
Spatter around the tip is okay. The front end of the contact tip not being even is also okay. The most important feature to check is the orifice of the contact tip and the coloration of the threads and base. If those look sound, your contact tip is likely still usable.
A bad tip is just the opposite. It's severely discolored, looks overheated to the point where it almost starts flaking. The orifice of the tip is no longer round or smooth. The wire micro-arcs inside of the contact tip. Your torch experiences burnbacks.
Contact Tip Summary
It takes a long time to wear a tip out. You should get multiple spools of wire on one tip, in most cases, if everything is set up properly, so your manual applications where the guy can manipulate that gun to direct that wire into the weld joint, a contact tip can last a long time before it starts to wear out.

The liner takes wire from the drive rolls and guides it through the gun to the contact tip.
All MIG guns have a liner. It is a wear item, and works to protect the internal parts of the welding gun.
Liners last for quite a while. The common reasons wire liners fail prematurely are:
- Improper length
- Burred or sharp edges
- Improper drive roll tension
- Using the wrong line type
- Wrong size wire liner
Wire Liner Length
The most common cause of a prematurely worn liner is cutting them too short. Conversely, you can never have a liner cut too long, because you will be able to fit the contact tip back into the holder.
Proper liner length depends on many factors. One to consider is whether the liner is design to float or held in place with a set screw.
For a floating liner, you want the contact tip once threaded into the diffuser to compress the liner back into the cable. This ensures the liner is snug to the entry point of the contact tip and there is no gap between the end of the liner and the starting point for the contact tip.
For liners with set screws, the maintenance process is more straightforward. Since the screws holds the liner inside the neck, you simply need to cut it to the right length after properly tightening the set screw. The most common issue with these is misplacing the set screw. Doing so make your liner then a floating liner, and you have to cut it to compress the contact tip into it.
Proper Liner Trimming
Liner trimming is a common cause for liner failure. Oftentimes it is not taking extra steps after cutting the liner to ensure a smooth wire feed.
When the wire liner is trimmed, make sure there's no burr or a sharp edge that points towards the internal side of the liner that can cause the wire to shave.
This trimming practice applies for both the power pin side and the contact tip side of the wire liner. The liner can fail in both spots with a burred or sharp edged liner. Properly trimming on both ends is crucial to a smooth wire feed and keeping the liner clean and maximizing its use.
Failing to cut the wire liner properly creates a lot of burnback or micro-arcing inside the liner from the gap created by a short cut liner, which causes it to fail.

Correct Liner Type
Wire liners come in many varieties and that can lead to using the wrong one often.
The key to choosing the right liner to pair it with your filler metal. For example, with everyday steel 70-86 type wire, utilize a steel liner.
If you use soft wire like aluminum, you will need to look at something Teflon-based or a combination-style wire liner. Smoother bored liners like Teflon or steel with brass inserts help with feeding aluminum wire, which tends to be abrasive and prone to shaving.
Abrasive wire acts as a saw blade on the liner, which can cause issues with wire feed, burnbacks, and micro-arcing.
We have a useful article of breaking down wire liners for wire types and their best uses here.

Wire Liner Pull Test
One useful way to check the liner to know if the wire liner is still good or bad is to perform a pull test.
A pull test is done by taking the following steps:
- Loosening or disengaging the drive rolls
- Lay the welding gun flat or with minimal angles
- Pull the wire through the welding gun by hand
A well-practiced rule of thumb is if you cannot pull the wire through by hand both the wire and the liner need evaluation.
You can do this test both before the feeder and after the feeder to ensure no obstructions within your liner. It’s also wise to check tension and perform a pull test from the contact tip to the drum or wire source.
Using a tension scale while performing this test will accurately measure the amount of tension of your wire. Performing a baseline test on a fresh liner and new wire spool will give you a proper frame of reference to judge other pull tests. A fish scale even works well in a bind where a tension scale is not available.
If you have a drum or a roll of wire down at base of a weld boom, you likely have 10 to 20 feet of conduit to feed wire through. It’s important to confirm wire tension and that the feeder is exerting minimal effort to feed.
If you do experience wire tension problems, additional equipment like wire straighteners help keep tension as low as possible and keep wire traveling reliably.
The goal is for the wire tension to be as minimal as possible. The right range varies greatly. For instance, proper tension can be anywhere from 8 to up to 20 pounds. Remember that there are many factors in play, different types of wire, and length of gun or length of wire.
Checking Drive Rolls
An important maintenance check item with wire liners is ensuring the filler metal and drive rolls match up in size and type.
Different filler metals require different drive rolls. There are several different types of drive rolls available. The standard for steel wire is a U-groove drive roll, for instance.
All drive rolls have grooves to fit a specific size wire. They are not one size fits all, which many people miss. If you use .035 wire, you should have and use .035 drive rolls.
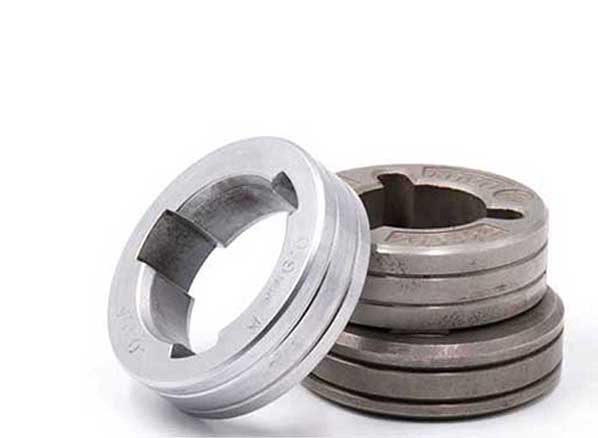
Drive-rolls are also typically dual sided. That means you have a side grooved for .035 wire or a side grooved for .045 wire. Sometimes getting the proper drive roll for the wire is a matter of flipping that drive-roll around to make sure you have the right drive roll or right setting on the drive roll for that wire.
If you have different wires, some require a V groove or knurled rolls that are serrated. Push-pull welding guns can use combinations of drive-rolls to get the right wire feed.
Check with your wire manufacturer or your feeder manufacturer and what drive rolls they specify for that type of wire. Your welding gun manufacturer will also have recommendations – especially if you using specialty torches like push-pulls.
Drive Roll Tension
It’s important to have the proper drive roll tension as well. I've witnessed several cases where drive roll tension is so tight it changes the size of the wire, forcing the wire to come off the spool or the drum a different shape.
If the drive roll tension is too tight, it can change the wire to a square wire or an oval shaped wire, which will cause issues with feeding through liner all the way down to the tip, wearing multiple component prematurely, but especially risks damage to the liner.
Trying to pull a bent-out-of-shape wire through the round orifice of a contact tip is a big drain on time and resources.
Wire Liner Connections
Everything on a MIG gun has connection points. The wire liner is no different.
The neck connection should be good and tight if you are using jump liners or neck liners in your welding guns.
Most MIG guns have a way to remove the neck, change out, or rotate the torch neck. These connections need to be tightly connected.
Ensure the main liner is of proper length and the neck liner, if used, mates or interfaces to that main liner properly. The neck liner should seat into the end of the wire liner without any gap in between.
Proper upkeep on a liner depends on keeping everything that touches the liner as clean as possible. You can blow the liner out with compressed air if you need to, but it's unnecessary so long as you keep the surface of the wire, the drum, the spool – anything comes in contact with that wire liner – clean.
After shift or when the day ends, doing simple things like putting a plastic bag over the wire roll can have a sizable impact on maintaining the integrity of the wire liner and keeping it from clogging or wearing prematurely.
You could also enact a practice like pulling that spool off every night and putting it in a cabinet to keep it from rusting. This would keep dust or moisture from accumulating on the wire.
Using drum protection gear like top hats keep debris from collecting on that wire. Anything that collects on the wire will push into the liner, and work to clog up or fill the liner full of debris.
Debris in the liner of any type causes feeding issues and arcing issues inside the welding gun.
Improper Liner Size
Just like with contact tips, it’s a common and not recommended practice to use an oversized wire liner to help feed wire. Also like with contact tips, it’s not a way to extend the life of the part.
All wire liners cover two sizes of wire, so .035 and .045 wire will fit in the same liner. Same with an .052 and .062 wire liner.
Running an .035 wire into a .062 liner, though it will work in theory, eventually will fold the wire into the liner due to the lack of column strength in the smaller wire. Any such restriction will cause the wire to immediately birdnest inside the liner. Birdnesting is one of the most time consuming and expensive welding gun maintenance tasks to do, and is a big drain on resources.
Take care to match the liner to the wire and to the contact tip. Mismatching sizes is certain to cause maintenance downtimes.

Keeping a Straight Wire
One note about wire and wire liner that isn’t often discussed is that when wire comes out of the drum or comes off the spool, it's has a natural cast or helix to it.
That helix typically forces the wire to go back to the natural shape it was in that drum or spool, which can cause it to rub against the coil of the wire liner. This shaves parts of the wire into the liner, clogs it, and contributes to it needing replacement.
A straight wire feeds easiest into a line and, by extension, into the contact tip. To increase liner life and even tip life, you can put a wire straightener on the back end of the feeder before that wire gets into the feeder itself.
Several manufacturers offer different types of wire straighteners. It's not an absolute necessity to use for proper wire feeding, but it will definitely help straighten wire and allow better feed-ability while improving both wire liner and tip life.
Always Replace Your Wire Liner
The purpose of a liner is to guide that wire through the gun to the tip. If you remove or replace the liner and try to pull your wire through the conduit gun, it might work. The way most guns are designed, there's a section in the cable where the liner specifically fits into.
That might be a 3/16 or a 1/4" conduit, which is a large opening for any liner to fit into. If there is no liner installed in your welding gun, it leaves a large void for that wire to bounce around and travel through.
The result of not having a liner is a lot of torch damage. Pushing the wire through the outside of the gun, or damage some of the other inner components inside of the cable are the most common results of not having a wire liner installed. It’s the most surefire way to ruin the welding gun.
The liner exists to protect the internals of the MIG gun, to feed that wire from the drive rolls to the contact tip, and to wear out the liner versus wearing out the internal parts of the gun or the neck.
Without a liner, the torch will experience internal wear, and the result will be a damaged and ruined MIG gun. Wire liners are a small cost to keep the rest of the torch running correctly. Make sure you always are replacing it when it’s worn.
Nozzles have a basic function and purpose. The purpose of the nozzle is to direct shielding gas flow, keep the gas centered in the arc and protect the weld from atmospheric conditions. Many times welders need different sized nozzles – smaller, larger, or tapered – for specific weld joints reaching tight access areas.
Most nozzles fail prematurely from:
- Using Rough Tools to Clear the Nozzle Out
- Overusing Chemical Agents
- Tapping or Hammering with the Nozzle
- Using Smaller Nozzles for Heavier Applications
Using Pliers & Welpers to Clean the Nozzle
Nozzles wear out more from cleaning and preventative applications than from actual usage. By cleaning it with a rough tool, you get spatter that sticks to the nozzle, especially in a short circuit process where spatter is more prevalent. This results in greater spatter adhesion to the nozzle, and cleaning more frequently to remove spatter off the nozzle. While this doesn't restrict shielding gas flow, cleaning spatter off frequently wears on the nozzle by scraping off the nozzle material while removing the spatter.
Many people use pliers or welpers to scrape weld spatter out, and they usually work pretty good even if they remove base material, as well.
Other ways to clean nozzles include using a die grinder or a file to gouge into the bore of the nozzle. Again, this type of maintenance does work to clear spatter, but it does wear the nozzle out.
Many times the spatter adhesion to a nozzle in a manual process is overcome by taking care of your process control. Small adjustments to amperage, gas flow, wire feed speed, drive rolls tension, etc. will do more to prevent spatter on the nozzle than using a chemical agent.

Overusing Anti-spatter Agents
If you go through all of the weld process improvements and still are experiencing spatter issues then utilizing an anti-spatter agent on the nozzle would be an option. Generally, I recommend using either a ceramic or silicone-based anti-spatter.
Use nozzle gel when it is the only option available. Nozzle gel usually brings more mess and problems because it creates a coating and a lot of dust and other particles stick to that coating. Like a wax, once it starts to melt, too much of it can seep and drip back down in the liner or clog the diffuser and obstruct shielding gas flow.
If you do use nozzle gels, know that gels are supposed to have a hot nozzle dipped into a very small part of that nozzle. This melts the gel to thinly coat the inside and outside of the nozzle. The nozzle exterior should use no more than half an inch of coating or dipping into the gel. The most common misuse and damage done to welding guns from nozzle dip is the welder burying the nozzle deep into gel jar and immediately filling up the diffuser ports. This will restrict shielding gas flow and cause porosity in welds.

Hammering with the Nozzle
It’s very common after cleaning out a nozzle that a welder taps the nozzle on the side of the table or side of the part to knock out any residual spatter.
Most small taps are not going to hurt anything on the MIG gun, but when you start banging the nozzle or using it as a hammer to fit parts up, then you start misshaping the nozzle and crimping the nozzle to the tip holder diffuser. It’s at that point you start ruining parts from misuse.
The most common issue from nozzle hammering, especially with a water-cooled welding gun, is breaking the insulators between the inner conductor tube and the outer protective tube. This causes the torch to arc inside the neck, which will then burn a hole through the neck and cause the torch to leak coolant.
Necks are overall durable because there is not a whole lot of pieces to them, but in a water-cooled application, you can do a lot of damage just by hammering or forcefully tapping the nozzle on a part to fit it up or the table to clear spatter.
Know that while the nozzle won’t be visibly damaged from hammering, other components will be damaged downstream in your welding gun from just a few heavy taps on the nozzle.
I highly recommend monitoring nozzle hammering habits from your welding technicians and try to teach it out of them if you want to reduce damaging your welding guns.
Nozzles Cracking or Breaking Down
In spite of all the areas I am recommending you take charge over, know that a nozzle can and should last an extremely long time.
But, nozzles can be prematurely worn from overheating. This occurs from using smaller nozzles for larger weld jobs.
Plated nozzles get overheated in cases where a smaller rated nozzle, like a 200 amp nozzle performs heavy welds, such as 400 amp welds. This will overuse the nozzle, overheat it, and it will begin to break down – normally the threaded inserts within the nozzle begin to come apart.
If your nozzles fail from the threaded inserts becoming undone, double check the nozzle rating against your weld parameters. Then verify the nozzle threads tightly to the diffuser or neck, depending on the torch.
Brass nozzles are more prone to fail because they are more brittle in nature. Other nozzle types that crimp the threaded insert or the threaded insulator in the nozzle do start to crack and fall apart when they exceed their rated temperature.
Basic Nozzle Maintenance
One tool that is not a rough tool and underutilized for cleaning nozzles is a tubular or cylinder-style wire brush. These are tools are normally used in plumbing to clean out the inside of copper piping, but they work very well for welding nozzles, too.
Any wire brush in the 1/2" to 5/8” bore range fits many manual welding gun nozzle quite well.
These tools are especially effective because they do not scrape any material off the nozzle, such as the plating or the nozzle metal itself, while effectively clearing out spatter.
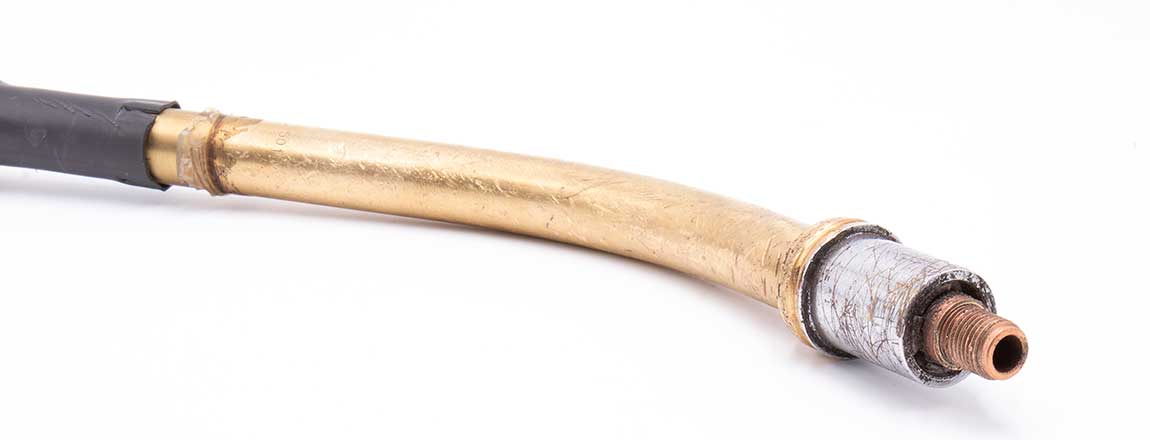

Rear connects and trigger leads are more downstream maintenance items for your Maintenance Manager. In truth, there isn’t a great amount of maintenance to be done on these components, but regularly checking these welding gun components will ensure your rear connect, also called the power pin, doesn’t contribute to holding back your welding productivity.
Rear connects are the connection that go inside the feeder and transfers weld current from the feeder power pin through the cable and to the contact tip.
O-rings will be your most common form of maintenance on the power pin. Depending on the power source, you could have any number of O-rings on the pin. Newer machines have usually two O-rings that seal off the gas fitting of the feeder and directs gas flow inside the gas hose of the welding gun.

If you do not regularly pull the welding gun in and out of the feeder, you will seldom have issues with the rear connect. But, if you commonly pull the MIG gun off the power supply every day or every few days, it is highly recommended you use basic O-ring grease regularly to ensure the O-rings are lubricated and not wearing from being constantly removed and installed into the power source.
Every few months is a good rule of thumb to check O-rings. As a wear item, they will dry out and crack if they are not regularly inspected and cared for.
Cracked and dried out O-rings allow gas flow to leak. Oftentimes welders compensate for that by turning up shielding gas. This ends up costing production more on the back end as you waste gas to get the same result. Investing the small amount of time to lubricate your rear connect O-rings will ensure proper gas flow and less wasted gas.
When you do remove the power pin – for other maintenance items like a wire liner change, make sure they’re tightly connected when they are re-installed. Because rear connects are not a moving part, they will not loosen up on their own unless they are loosely connected or forcefully pulled.
If the power pin isn’t tightly fastened to the power source, the most common failures that will occur will be:
- High resistance
- Loss of Current Transfer
- Arcing at the Rear Connect
Loose connections like this most commonly happen when the welder or the maintenance manager is hurried when making a part replacement or ensuring a connection and fails to tighten the clamp to hold the power pin into the feeder.
This means that other forces like either gravity or the push of wire through, slide the power pin out of the feeder. A situation like that will cause arcing issues and risk ruining the power pin or even the feeder connection. That will result in issues that are more serious in downtime and costs.
Trigger Leads
On the power pin is also the trigger leads. These are what control the feeder of the wire from the power supply to the contact tip.
For these connections, it is about making sure they are tight. The most common damage done to the trigger connector is removing the welding gun and forgetting to unplug the connector and tearing the cable out or damaging the pins.

Know that when you do install the trigger lead, there is a detent in that connector to the feeder. Make sure the male end fully engages into the detent to ensure a tight connection.
The amp connector that goes into your feeder on most single schedule guns uses two pins. They will either be labeled Pins A and B or Pins 1 and 2. If a cable fails, there are normally spares you can use. I would recommend checking the operator’s manual on your welding gun to for specific instruction on fixing a broken trigger lead, because they can vary.
The cable is the main part of that gun that connects the front end to the back end. It’s the primary carrier of current, gas, and wire. Cables are largely an afterthought for the welder as it’s often out of sight while performing their job.
There’s no getting around weld cables. They often wear, cut, or pinch after a certain amount of use. And the problem with cables is they often are not something you simply repair or do maintenance on because of OSHA and safety guidelines.
Once a cable is no longer usable, it has to be discarded or replaced entirely.
You can take a few steps to ensure you do everything within your power to avoiding cable cuts and abrasions by following a few simple preventative steps.
Proper Cable Lengths
First is to make sure you are using the properly sized cable for your welding process. For most MIG gun makers, a 15-foot cable is the standard, and for good reason. It’s often the right length for almost any job.
Often, production lines will use welding guns that are either too short or too long for their job. A 25-foot welding gun, for instance, is very long and not always needed. Guns with cables that length are more likely to get in the way, loop around table legs or parts, and can cause wire feed issues which will cause your liner to wear prematurely.
If you use a 25-foot MIG gun in your plant, see how often every foot of that cable the welder uses to reach the part. If you can, use a shorter cable. It will save you on cost and lessen the amount of wear to internal component like the liner.
A welding gun cable that is too short is a similar cable hazard. Shorter welding cables will pull the power source. This will cause unnecessary strain and damage to the trigger leads and power pin. Using a welding torch with too short a cable will pull apart and wear on the cable connections.
Much like monitoring long welding guns, look at whether your shorter length MIG gun drags the power source and puts stress on the power pin. If you notice your welder having to drag the power source with them, you should consider a longer length welding gun.
Cable Placement
The easiest way to extend the life of your cable without replacing it or evaluating it is making sure your weld technicians keep the cable out of the way whenever there are moving parts of equipment on the shop floor. There’s been countless times over my preventative maintenance trainings with fabricators where welding gun cables are damaged from a beam rolling over it or a part comes off the crane and is put on the floor and a part of the welding torch cable is sticking out and ends up being landed on.
This will dent or crimp the welding cable. Taking measures to keep the cable out of the way when moving parts are around is a surefire way to prevent them from premature damage.
Tight Connections
Remember this? Just like every other component of your welding gun, making sure your cable connects securely to both the front end and the rear housing will keep current steady and prevent any premature damage.

Preventative Weld Cable Covers
There's several different types of cable covers out there, all made with different kinds of material. They do a good job prolonging the life of the welding gun cable when installed properly.
An ideal welding cable cover will suit the job and not add a lot of weight to the welding gun.
Kevlar, leather, or Denier Cordura material all are helpful cable covers that can protect your cable from wear on the shop floor.
Find a cable cover that suits the need and doesn’t add a lot of weight.

The neck of your welding gun is the component that directs wire and assists in the current transfer to the contact tip.
Like every other component of your welding gun, the torch neck is a very durable part when it’s not used in a way it shouldn’t be. Since its primary purpose is to direct wire, using it as a hammer to fit up parts will break components within the torch neck.
For water-cooled welding guns, the first component to break if you damage the neck will be the insulators. Once that happens, the torch will begin to arc internally and create leaks inside the neck. If your torch doesn’t leak, it will at the very least cause connection point issues between the cable and the neck, which will increase resistance and cause current transfer problems.
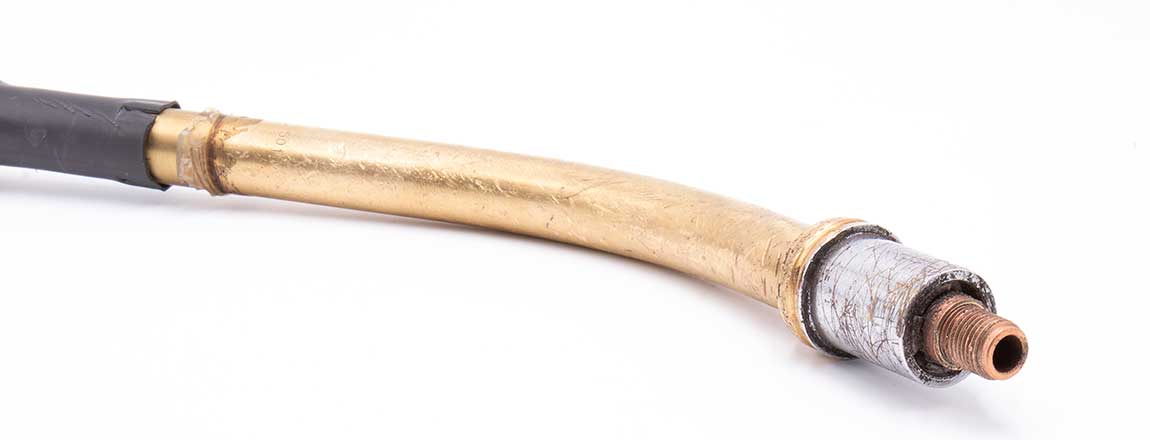
For air-cooled necks, there are insulators separating the inner and outer tube from becoming electrically hot. Hammering on the torch neck or the nozzle can break those insulators and cause an electrical hazard on the neck. Pinching or denting the neck from hammering the front end to clear spatter or fit up parts will also increase wear on the wire liner and cause the torch neck to arc out. Even with less components to damage, air-cooled necks can fail if abused on the job.
Other issues with the torch neck from bad practices like torch hammering include misaligning the inner tube from the outer tube. This will cause the contact tip to no longer be centered within the nozzle. It’s easier to cause this type of damage on fume extraction torches or water-cooled torches, but damage like that does have an effect on gas coverage and risks weld porosity.
Basic Torch Neck Maintenance
Water-cooled necks are the only style of manual welding gun where you will need preventative maintenance. You’ll find in many of these style torches O-rings on the necks. These rings, like the ones of the power pins, need lubrication periodically to prevent them from drying out or cracking.
Most welding equipment makers supply O-ring repair kits, or spare O-rings kits to replace those O-rings needing replacement.
I would always suggest a little bit of O-ring lubricant. It is sure to prolong the life of the O-rings and keep the torch neck from needless damage from coolant leakage.
You always want to be making sure you’re getting the most mileage possible from your welding equipment. It is for sure a big investment, and you want to get sure your team is being as productive as possible while also safeguarding equipment investments.
Taking proper care and doing welding gun maintenance the right way may mean some departures of past behavior, but even making small tweaks in your daily equipment checks or monthly maintenance items can mean far less spent on consumables, less new equipment needing to be purchased, and adding more profit to the bottom line.
Having a detailed welding gun maintenance program that you can get all of your welding technicians to buy into may have its ups and downs when getting started. But with patience and attention to detail, you will undoubtedly save on equipment cost and find your production line getting more parts made and built faster and for less.
The key is being consistent and monitoring good practices.