Tungsten electrodes
Wherever finely crafted weld seams are created, high-quality materials are welded and precisely welded joints are to be created, TIG welding is required – and good tungsten electrodes. With tungsten inert gas welding (TIG), in addition to the torch, the power source and the shielding gas, the non-melting, temperature-resistant tungsten electrode is an essential factor for optimal results.
The range of TIG welding electrodes is very extensive. At the latest when it comes to choosing the right TIG electrode for your own welding task, you will be confronted with colour coding of the tungsten electrodes. The individual electrode types are marked with different colours.

As the name suggests, the main component of tungsten electrodes is tungsten. With the exception of the green TIG welding electrode made of pure tungsten, all the others are made with oxidic additives such as zirconium oxide, lanthanum oxide, cerium oxide or thorium oxide. Others contain oxidic additives with rare earths. You will find their effect and properties under »TIG welding electrodes and their color coding or doping« on this page.
When choosing the tungsten electrode, the following aspects must be taken into account:
- Tungsten electrode type
- Electrode diameter
- Grinding quality and roughness of the electrode
- Tip geometry of the TIG welding electrode
All information at a glance
- TIG welding electrodes and their color coding or doping – tungsten electrode types
- Grinding quality and roughness of the electrode
- Tip geometry of the TIG welding electrode
- Finding the right TIG tungsten electrode
- Blogs about TIG welding and tungsten electrodes
- Video tungsten electrodes
- Documentation
TIG welding electrodes and their colour coding or doping – tungsten electrode types
E3® PRO
The E3® PRO tungsten electrode with the color code purple & gold can be used for all processes. It is a further development of the successful E3® from ABICOR BINZEL. Thanks to its special composition of rare earth oxides and a newly developed manufacturing process, its structure is particularly fine and homogeneous. As a result, it has even better ignition properties – in the low ampere range these are even significantly better – and has an even longer service life than its predecessor. The E3® PRO TIG electrode can be used with direct current as well as alternating current, for manual welding as well as in automated applications. In addition, the E3® PRO is absolutely non-toxic for people and the environment. If you want to play it safe when TIG welding, the E3® PRO is a tungsten electrode that can be used for all applications and materials.
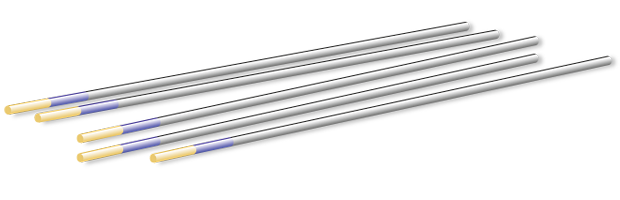
Color coding with rare earths:
- Gold-Purple = E3® PRO
E3®
The tungsten electrode E3® (purple) developed by ABICOR BINZEL with oxides of rare earths as doping elements is suitable for both direct current (DC) and alternating current (AC) welding. Practically any metal can be welded with it. Because of its excellent ignition properties, it is therefore also often used for automated processes. During the welding process, the electrode temperature remains consistently low, which in turn ensures better current carrying capacity and a longer service life compared to thoriated electrodes. The latter may only be used in exceptional cases because of their extremely harmful effects.
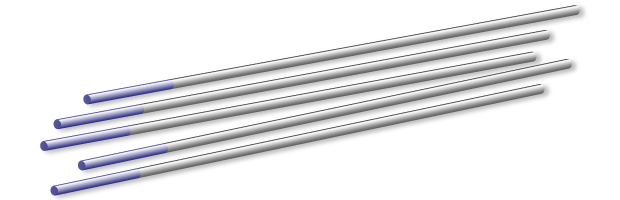
Colour coding with oxides of rare earths:
- Purple = E3®
WLa
This tungsten electrode is mainly used for welding unalloyed and high-alloy steels, aluminum, titanium, copper and magnesium alloys. Its doping element, lanthanum oxide, makes it suitable for direct current as well as alternating current welding, just like the E3®. The golden TIG welding electrode is also used in micro-plasma welding.
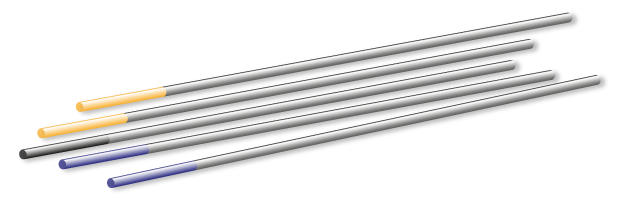
Colour coding with lanthanum oxide:
- Black = WLa 10 – with 0.8 to 1.2 % lanthanum oxide
- Gold = WLa 15 – with 1.3 to 1.7 % lanthanum oxide
- Blue = WLa 20 – with 1.7 to 2.2 % lanthanum oxide
WCe
The doping element cerium oxide makes this TIG welding electrode more resilient than an electrode with pure tungsten – but less than the E3® and lanthanum electrodes. This type of tungsten electrode is used primarily in the medium and lower current range for welding unalloyed and high-alloy steels as well as aluminum, copper, nickel, titanium and magnesium alloys. They can be used for both alternating current welding and direct current welding – however, less well than the E3® electrode from ABICOR BINZEL.
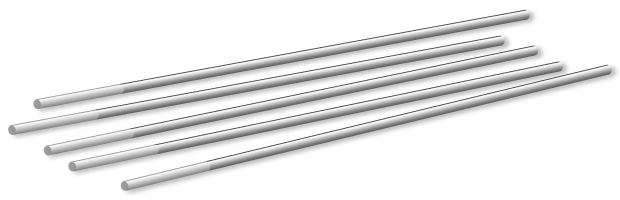
Colour coding with cerium oxide:
- Grey = WCe 20 – with 1.8 to 2.2 % cerium oxide
WP
The green undoped tungsten electrode was developed for welding with sinusoidal alternating current especially for light metals. It is not suitable for direct current welding. As the green pure tungsten electrode prevents the formation of a pure square wave due to its inertia and high work function, it is not recommended to use this welding electrode with inverter power sources. The ideal replacement for the green tungsten electrode is the E3®.
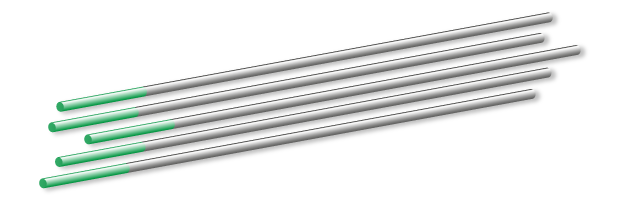
Colour coding with pure tungsten:
- Green = W – made of pure tungsten without any oxide component
WZr
With its doping element zirconium oxide this tungsten electrode reduces the risk of contaminating the weld pool. This TIG welding electrode is mainly used for AC welding, because it is not only suitable for DC welding to a limited extent. In AC welding, this doping element ensures a very stable dome. On the other hand, a tungsten electrode with zirconia does not ignite as well.
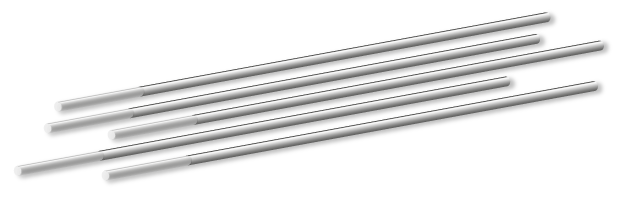
Colour coding with zirconium oxide:
- White = WZr 08 – with 0.7 to 0.9 % zirconium oxide
Grinding quality and roughness of the electrode
Before a tungsten electrode can be used, it must be ground, because in addition to the grinding quality, the grinding direction affects the arc. Important when grinding the TIG needle: The grinding direction must be longitudinal (axial) to the electrode! A bevel in the transverse direction (radial) to the TIG welding electrode causes a very restless, unstable arc. In addition, if incorrectly ground, the smallest tungsten particles can get into the weld pool and contaminate it. An axially ground tungsten electrode has good ignition properties, a stable arc and favorable electron emission.
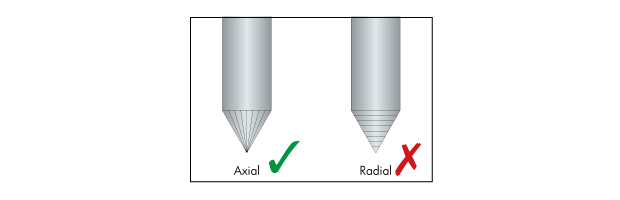
Tip geometry of the TIG welding electrode
Both ABICOR BINZEL all-rounder electrodes for TIG welding E3® and E3® PRO produce the best welding result if they are ground at an angle of 60 degrees and used in the intended current range. More acute angles of around 30 degrees are more suitable for the lower current range. In this case it is better to switch to a thinner electrode.
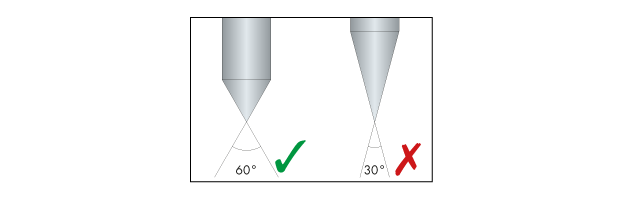
With a more obtuse grinding angle of 60 degrees, a narrower weld pool, a high current carrying capacity and longer service life can be achieved.
Finding the right TIG tungsten electrode
The table below shows the most common types of tungsten electrodes, including their suitability and properties. This overview will surely help you to find the right TIG welding electrode for your own welding process.
The illustration clearly shows that the E3® as well as the E3® PRO can be used universally and have the best properties in all directions:
E3® PRO | E3® purple |
WLa 15 gold |
WLa 20 blue |
WCe 20 grey |
WP green |
WZr 08 white |
|
gold-purple | |||||||
Direct current minus pole | +++ | +++ | ++ | +++ | + | – | – |
Alternating current | +++ | +++ | + | + | + | + | ++ |
Arc stability | +++ | ++ | + | ++ | + | – | ++ |
Ignitability | +++++ | ++++ | ++ | +++ | + | – | + |
Lifetime | +++++ | ++++ | ++ | +++ | + | + | ++ |
High alloy steels weldable | ++++ | ++++ | +++ | +++ | +++ | – | – |
Aluminum weldable | ++++ | ++++ | + | + | + | ++ | ++ |