Correct maintenance of MIG/MAG welding torches – Basic knowledge and helpful tips
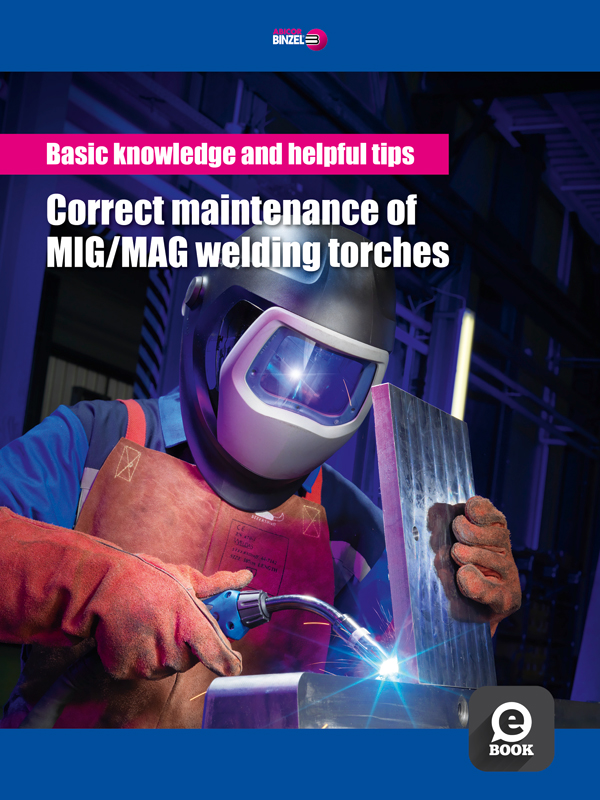
A manual for welding specialists
MIG/MAG welding torches have to go through a lot in their lifetime. The individual components of the torches are exposed to very different loads. A manual torch should be productive, produce high-quality welds and weld for as long as possible – without premature interruptions due to, for example, wire sticking, leaks, power transmission failures or the replacement of individual wearing parts such as gas nozzle, contact tip, nozzle holder etc.
In this e-book we have compiled everything you need to know about the correct handling and maintenance of MIG/MAG welding torches:
- Causes and solutions for the partially premature wear of spare parts
- First aid tips in case of welding torch failures
- Preventive measures for a long torch service life
- Tips for replacing wearing parts
- Checklists for the prevention of malfunctions
This e-book is a valuable manual for welders. It contains detailed descriptions as well as clearly summarised information covering all the essential parts of a manual welding torch, from the gas nozzle to the machine-side connection of the cable assembly.
... or scroll down to read the full manual.
Enjoy!
- About the authors
- Introduction
- Checklist: before starting welding
- Gas nozzle
- Contact tip
- Welding torch neck
- Cable assembly for MIG/MAG welding torches
- Liners
- Characteristics of different welding wires
- Characteristics of different liners, wire liners & co.
- Tips for handling liners
- Wire sticking – a problem with many causes
- Wire feeder connections as an error source
- Cutting the liner correctly to size
- Lack of pre-dressage of the wire
- What you need to know about drive rollers
- Machine side connection & control cables
- Editorial team

Boris Rinn
Product Manager MIG/MAG Manual Products, ABICOR BINZEL
Boris Rinn is Product Manager for manual MIG/MAG products and machine torches at the ABICOR BINZEL headquarters in Buseck. After training as an industrial mechanic, he completed a degree in mechanical engineering at the Technische Hochschule Mittelhessen (technical university) and today brings all his technical knowledge into the broad field of manual welding.

Prof. Dr.-Ing. Emil Schubert
Technical Director CTO, ABICOR BINZEL
Emil Schubert, professor in the field of production engineering with a focus on thermal cutting, welding and surface treatment, has a doctorate in laser material processing and has worked in welding technology for over 20 years. Emil Schubert has been Technical Director at ABICOR BINZEL since 2008 and is also active in a wide variety of expert panels and working committees.
MIG and MAG welding torches are constantly exposed to heat and radiation, attacked by weld spatters and are often misused as hammers, for example. They are required to perform at their best, regardless of whether they are used in a small workshop or in a harsh industrial environment. They are an everyday work tool that you want to be able to rely on, and must, even when “things get hot”. This makes proper maintenance of welding torches even more important, as this can extend their durability and thus their service life. Especially today, where time is more precious than ever before.
This e-book is all about the good care and maintenance of MIG and MAG welding torches and their consumables – from the contact tip and gas nozzle directly at the process to the torch neck and wire feeding, through to the wire feeding rolls in the wire feed unit of the power source.
This e-book is intended to provide users, welding specialists, welding supervisors and production managers with an overview of the proper maintenance and care of MIG/ MAG welding torches, so that production costs can be kept low and quality and output correspondingly high. It shows how good, regular maintenance significantly extends the life of a welding torch, and thus ensure that its performance level is maintained at a constant level.
Please use this e-book as an introduction to the maintenance of MIG/MAG welding torches. Make it easy for yourself to identify problem areas, prevent premature failures and individually adapt the handling of the torches.

The following components are subject to preventive care and maintenance measures and are highlighted in this e-book:
- gas nozzle
- contact tip
- torch neck
- cable assembly
- wire feeding
- machine connection and control cable
If you consult this information and the tips for the preventive care and maintenance of your MIG and MAG welding torches, and implement them, you will certainly enjoy your torches and the welding result for a long time.
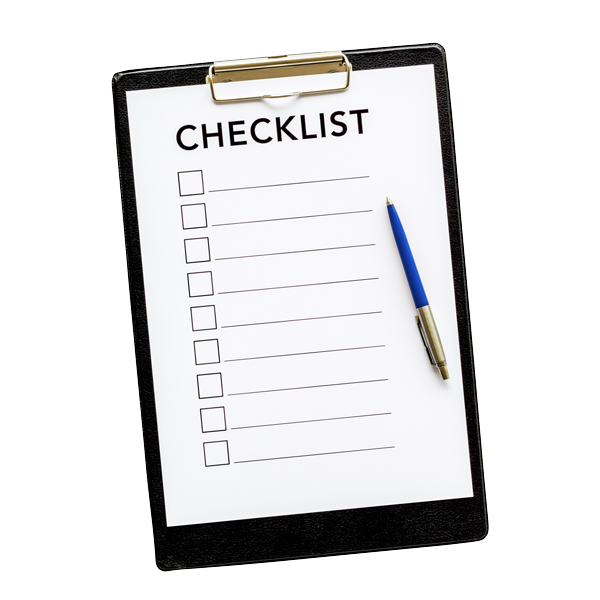
A few hints, simple tasks and regular checks around the MIG/ MAG welding torches can noticeably extend the service life of wearing parts and thus of the entire system. Often the little things make a big difference. On the following pages we will discuss the above mentioned wear parts of an MIG/MAG welding torch and start with the part that is at the very front and closest to the process: the gas nozzle. Based on the construction of a welding torch with torch head and its wear parts, via the cable assembly to the machine-side connection, to the wear part wire feeding roll in the feed unit, we will go through all wearing components and show what can happen during the process in daily use. At the same time, we will provide tips on maintenance and care, so that the system can be used for as long as possible and without restrictions.
To the point
The following short check should be carried out every day before the start of work
1. Is the torch connected correctly?
- The central connection is connected tightly.
- Any existing control cables are connected and the mounting ring is turned to its lock.
2. Is the torch reconnected or are you taking over a workstation whose condition you cannot be 100% sure about?
- The performance specification of the torch matches the welding parameters.
- The liner matching the wire material and the wire diameter is installed in the torch. To check, loosen the nut on the machine connection and pull the liner out slightly.
- The O-ring on the central connection is undamaged and sufficiently greased.
3. Does the cable show damage, cuts, breaks or pinches and does the torch need to be replaced and possibly repaired?
4. Is the torch neck bent or does it have any significant impact marks? If these are visible, the torch must be repaired and possibly replaced.
5. Is the gas nozzle ready for use? Please disassemble to check.
- Check the inside of the gas nozzle for impurities by weld spatters and remove them if necessary. You must replace the gas nozzle if it is bent or has heavy splash adhesions that can no longer be removed.
- The bore on the contact tip holder or gas diffuser are free and not contaminated by weld spatters.
6. Check the contact tip.
- The right contact tip for the wire diameter used is fitted. Check the state of wear. If the bore is oval “eroded”, it must be replaced.
- Strong discoloration due to overheating also requires replacement. Check if the contact tip was tightened correctly. If it was tightened, check whether the welding parameters match the specifications of the torch, or whether it is possibly overloaded. For liquid cooled torches, check the cooling circuit.
7. Finally, check the tight fit of the contact tip, contact tip holder and gas diffuser and reassemble the gas nozzle.
8. Especially for liquid cooled torches:
- The coolant supply and return lines are connected to the machine.
- The coolant lines are undamaged and are not buckled or pinched.
- The coolant level is fine. Check this at the viewing window of the machine.
- If the torch is reconnected, make sure that the coolant has sufficient lead time. With a long cable assembly of 5 m, it can take up to 20 seconds for the torch to be filled with coolant and completely vented.

The task of the gas nozzle is to guide the shielding gas evenly with a laminar flow so that the arc and the weld pool are protected from external influencing factors, such as ambient oxygen. Another task is to dissipate process heat as quickly as possible and discharge it into the cable assembly or, alternatively, to block the heat in order to protect the torch neck, handle and cable assembly from too much heat. This depends on the basic design of the welding torch.
The welder always uses a gas nozzle that, on the one hand, is large enough to optimally fulfil its task of gas coverage, but, on the other hand, is small enough to ensure an adequate view of the process and good accessibility. Welders use gas nozzles of different sizes and shapes, depending on accessibility and application. Cylindrical gas nozzles enable the widest gas coverage. Better accessibility is ensured with conical gas nozzles that taper towards the front. Strongly tapered gas nozzles are best suited for tight seam preparations, and bottle-shaped or strongly conical gas nozzles are the best choice for narrow gap welding. The bottom line is that there is a suitable gas nozzle for every weld seam and every accessibility.
Reasons for gas nozzle wear
Gas nozzles are the wear parts that are closest to the process and thus the most exposed to heat, radiation and mechanical stress. These conditions are only one influencing factor on the service life of a gas nozzle. Another major influencing factor is weld spatters, which are an unavoidable part of the MIG/MAG process. Although they can be reduced by optimising the process parameters – they can never be 100 percent avoided. They can stick or burn on in the gas nozzle and other wear parts, such as contact tip, tip holder and gas diffuser.
The base material of most gas nozzles is copper, or a copper alloy. Gas nozzles made of brass usually have a shorter service life and dissipate heat poorly. Copper is an excellent heat conductor and is easy to process. At the same time, copper is very resistant. If heat is absorbed via the gas nozzle, a copper gas nozzle also dissipates it quickly, which generally increases its service life. If an insulated gas nozzle is used – with a high-temperatureresistant plastic insert – the heat is blocked in the front end and inadmissible heating of the torch neck, the handle and the cable assembly is avoided in this way.
Gas nozzle coatings such as a nickel alloy act as a separating layer to the base material and ensure that weld spatters are not burnt in or adhere so quickly. In addition, a nickel coating reflects light and heat and thus additionally reduces heat absorption from the welding process. The cooler the gas nozzle, the lower the spatter adhesion, because these either do not stick at all or can be easily detached. Coatings also increase the service life of the gas nozzle. Alternatively, or in addition to coating, a release agent can also be applied to reduce spatter adhesion.

A well configured welding process that produces as few weld spatters as possible ensures the basis for a long service life of the gas nozzle – and at the same time the wear parts used with it, such as contact tip, tip holder and gas diffuser. Each type of arc used in MIG/MAG welding – the three most common are short arc, spray arc and pulse arc – has an impact on spatter.
The impulse arc is the best way to control the welding process, because here a drop of the welding additive dissolves with each pulse current and passes smoothly into the melt pool. It has the lowest spatter formation but is demanding at high arc power in terms of the heat load on the gas nozzle. Here it is often recommended to choose a liquid cooled torch with a two-part cooling system, in which a cooling circuit is provided for cooling the gas nozzle, e.g. ABIMIG® GRIP W 555 D.
In case of short arcs and spray arcs, fine droplets separate when the wire is melted. The materials distributed by short circuit (short arc) and by the action of high currents and without short circuit (spray arc). Please pay particular attention to regular cleaning of the gas nozzle. In the case of spray arcs, a higher heat load of the gas nozzle occurs compared to the short arc, due to the higher currents.
The choice of arc depends on the thickness of the sheet to be welded and the welding speed. Special arcs under these three types of arcs reduce the accumulation of spatters. However, this requires a lot of knowledge, skill and sensitivity for the entire welding process. You can find out more about this in the blog “Cause of weld spatters: MSG welding and arcing”.
The gas nozzle must be regularly freed from weld spatters, because a gas nozzle that is heavily impacted by weld spatters can lead to quality problems, which in turn entail rework costs. Fixed weld spatters impair the flow of the shielding gas, and the protective gas shield over the weld pool is no longer adequate. Because of the resulting turbulence, oxygen and hydrogen can reach the weld site from the ambient air.
n extreme cases – especially with small gas nozzle diameters – weld spatters can build up to such an extent that they can lead to a spatter bridge with a short circuit. The welding torch can be damaged or even destroyed.

Spatter bridge between gas nozzle and contact tip due to heavy contamination
Anti-spatter agents for pre-treating gas nozzles
The right chemical separating agent
Even with optimal workpiece preparation, the attachment of particles cannot be avoided in the long term. An additional preventive care method is to spray the gas nozzle with an anti-spatter spray or to immerse it in a pasty non-stick agent before welding.

The ceramic spray from ABICOR BINZEL is suitable as a anti-spatter spray only for the gas nozzle or the front end of the welding torch. Once sprayed with the help of the coating cap, a so-called multilayer ceramic layer is specifically distributed on the sprayed wear parts and forms an excellent, long-lasting protective layer against hot welding particles. Adhering particles can be easily removed by gently tapping the torch head. Ceramic spray may only be applied to a cold torch.
Düsofix, the anti-spatter paste, is a release agent for immersing the gas nozzle for example. Functionally packed in a stable metal can, it can be placed anywhere within reach of the welder and defies even harsh working conditions. Simply immerse the hot gas nozzle in the anti-spatter paste and the gas nozzle and contact tip are optimally wetted with release agent. Important: immersing a cold torch can lead to clogging of the gas channels, resulting in uneven gas distribution, with the quality defects described above.
The Super Pistolenspray NF from ABICOR BINZEL is an anti-spatter spray for the gas nozzle AND the workpiece, as well as the clamping elements. This spray minimises spatter adhesion. The letters “NF” stand for “non-flammable” and mean that this welding protection spray meets the highest possible safety requirements. In addition, this release agent can be over-welded on the workpiece, thus facilitating fast further processing and saving additional time.
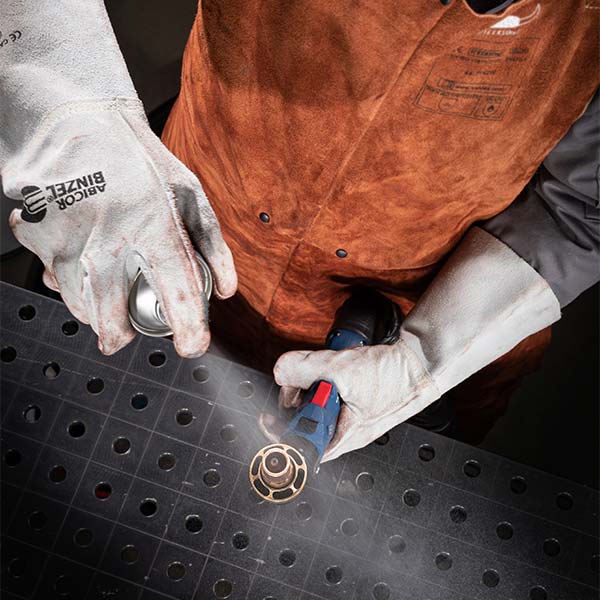


Careful handling of cleaning tools
Welders like to use so-called cleaning pliers. These are inserted into the gas nozzle and rotated, thus removing adhering particles mechanically. However, one disadvantage of this method is that the scraping not only removes weld spatters, but also removes the base material of the gas nozzle body piece by piece. The inner wall of the gas nozzle becomes rougher with each use of these pliers, and particles from the welding process adhere even more easily. As a result, the gas nozzle wears out faster. Anti-spatter agents facilitate cleaning and often prevent weld spatters from adhering very tightly, thus requiring the use of pliers and heavy scraping. Instead of pliers, a stainless steel brush can be used, whose soft bristles avoid scratches in the gas nozzle.

Damaged gas nozzle
Torch necks have a robust construction, as they do not consist of many individual parts. Tapping the torch head lightly on the edge of the table or workpiece to remove weld spatters will not harm the gas nozzle and is common practice among welders. However, firmer beating, or even improper use of the torch head as a hammer, will deform the gas nozzle and can damage internal parts such as the tip holder, gas diffuser and insulator.
Knocking may not cause visible damage to the gas nozzle, but other parts in the welding torch can be damaged by a few powerful blows to the nozzle. This should always be considered if you want to tap weld spatters off.


Bent mount of the contact tip holder
Basically, well-made and professionally manufactured gas nozzles are very durable. However, overheating is another cause, which is why gas nozzles must be replaced prematurely. This happens when torches are used that have less power than the welding process dictates.
The gas nozzle of a torch that is specified for a load up to 200 A will overheat when welding work is carried out at 400 amps. Possible consequences here range from shedding of coatings, through damage to the thread and, in the end, failure of the gas nozzle. In most cases, an overload can be easily recognised by the discoloration of the gas nozzle.
To the point
Causes that often lead to premature wear of the gas nozzle & first aid tips
1. Poorly adjusted process with high spatter formation.
- Adjust the welding parameters as optimally as possible.
2. Inadequate cleaning and pre-treatment of the workpiece – increased spatter.
- Before welding, always ensure that the workpiece is free of residues or deposits from previous work steps.
3. Coarse tools are used to clean the gas nozzle – damage to the coating. Weld spatters can adhere more easily to scratches.
- To prepare the gas nozzle, use only suitable chemical agents to reduce spatter adhesion. Attached weld spatters are then all the easier to remove.
4. Workpieces are straightened by tapping or hammering with the gas nozzle – deformation of the gas nozzle or even the entire torch neck.
- Avoid misuse of the manual welding torch and its spare parts.
5. Welding torches and gas nozzles that are not designed for this output are used for high currents – the gas nozzle gets too hot.
- Always use a welding torch that is designed for the application.
The contact tip – also often called the contact tube or contact nozzle – is the smallest and at the same time the most heavily used wear part of an MIG/MAG welding torch. It is equally used in manual torches, machine torches and robot welding torches, and is responsible for current transmission. It also feeds the wire and guides it into the welding process. It is sometimes even said that the contact tip is the heart of a MIG/MAG welding torch.

Similar to gas nozzles, there are also great quality differences in contact tips. Since these are wear parts that have now become a mass-produced item, you can find contact nozzles of different material quality and processing quality on the market for welding accessories. However, both have a significant influence on the service life and thus availability of the welding torch, and thus on the entire welding process.

The contact tips material for welding usually consists of E-Cu (electrolyte copper) or CuCrZr (copper-chromium-zirconium). In order to achieve very long service lives, special variants such as HDS (Heavy Duty Silver) contact tips from ABICOR BINZEL are also used. These have an inner core of particularly solidified copper and thus greater hardness than, for example, E-Cu. In addition, the silver coating reduces spatter adhesion.
E-Cu contact tips ensure very good power transmission and good heat conduction as well as electrical conductivity. They have very good process properties, but are less wear resistant.
CuCrZr contact tips are very hard and thermally highly resilient, due to the alloying elements chromium and zirconium. Their current transition, on the other hand, is slightly poorer. They offer good process properties with a low degree of wear.

Inferior contact tip:
Rough surface in the bore area

High-quality contact tip:
Smooth surface in the bore area
HDS contact tips have greater hardness, due to their special inner core, and are therefore extremely heat resistant. They are in demand at high currents and/or a high duty cycle, where CuCrZr contact tips sometimes reach their limits.
There are great differences in the prices for contact tips on the market – including in terms of quality. Cheap contact tips are usually made of inferior copper with a low degree of purity, which has poor thermal and poor electrical conductivity due to its lower hardness. This can lead to premature wear. Brand manufacturers, on the other hand, have a certified manufacturing process that is constantly monitored and only permits high quality material for the production of contact tips. For example, ABICOR BINZEL always offers consistently high quality with the high-speed deep drilling process.
High quality contact tips are characterised by their overall geometry, a precise, centred hole with a good surface and the well worked threaded connections.
But even an excellently worked contact tip made of good material wears out over time – especially since, depending on its use, several kilometres of wire a day can run through a contact tip. Although there are wires that do not wear the contact tip out so quickly, in the end they all wear out and need to be replaced.
Signs of wear and tear in contact tips and their causes
A worn contact tip shows different characteristics: changes in colour or shape due to excessive deposits of weld spatters, ovate or oval hole openings due to abrasion of the material by the wire, unevenness at the bore opening through to clogged holes.
Wire sticking
Contact problems often occur in the contact tip when straight torch necks are used, as is often the case in machine torches or robot torches. When wire drums are used, the problem is increased by the lower swirl of the wire. Because the contact surface and the contact time are too small, so-called micro-arcs are created within the contact tip. These cause faster wear of the contact tip. This can lead to the process becoming unstable. In such a case, a so-called burn back of the wire to the contact tip can easily occur. The wire ignites an arc in the contact tip instead of on the workpiece and merges with the inside of the contact tip. As a result, sticking occurs and the contact tip can no longer fulfil its task. If there is a conductive connection between the wire and the material to be welded, this can even lead to a short circuit and the complete welding torch can be destroyed. With the newer generation of power sources, however, there is no longer a risk of short circuit caused by welding spatter.
Bended torch necks help to minimise or completely avoid the above mentioned problems.
If wire sticking occurs more frequently, it may be that the contact tip is not suitable for the wire diameter. Some companies use contact tips that are too large for some welding applications. They want to reduce warehousing costs or keep them manageable and provide larger contact tips for some applications. It is not uncommon for two different wire diameters to be used at a welding workstation to weld a workpiece – but only one contact tip size is used. However, a practice like this does more harm than good, because more frequent changes of the prematurely worn out contact tips shorten the service life. The times for the removal of possible burnt-in wire and the shortened service life increase the costs.
A high-quality contact tip – whether made of copper or a copper alloy – should be able to weld several kilograms or several rolls of wire. If this result is not achieved, it is recommended to check the application.
Oval/ovate bore
If the contact tip bore is no longer round, but ovate or oval, it is very likely to have been in use for a long time. This form clearly shows one-sided wear and tear or abrasion by the wire feeding. Welding wire is either wound onto spools or placed in drums as so-called endless wire. Each wire bent in this way has a natural swirl that constantly rubs and removes particles when entering the contact tip. Even with the best preparation of the wear parts with anti-spatter spray, they are protected against spatter adhesion, but not against constant abrasion by the welding wire. As soon as the contact tip bore is no longer round, the contact tip should be replaced, because it no longer transports the wire into the process as precisely as desired.

Discoloration of the contact tip
Any kind of pure discoloration on the contact tip body testifies to strong temperature effects, e.g. due to excessive heat. In this case the thermal load capacity was reached or exceeded.
A violet-blue discoloration of the contact tip thread is an indication that high temperatures must have applied here. Overheating of the contact tip is caused if it is not tightened enough on the tip holder or gas diffuser, the current can only be transmitted poorly due to the high resistance, and the heat cannot be dissipated. The material of the contact tip is damaged by too high temperatures. For this reason, an insufficiently tightened contact tip runs the risk of wearing out prematurely.
The contact tip should be tightened with the help of a suitable tool, such as the ABICOR BINZEL multiple key. For transmission of the current and removal of heat, it is important that the contact tip is flat on the heel to the tip holder, and that the threaded flanks have sufficient contact.

Clogging/plugging of the contact tip
In particular with softer wires, but sometimes also with copper-plated solid wires, material is constantly rubbed off when the wire is transported through the cable assembly. Over time, this reaches the contact tip and can clog it. The wire transport is then braked or, in extreme cases, stopped and so-called wire nests occur in the area of the wire feed, as more and more wire is fed. However, a stuttering wire can also lead to wire sticking. The remedy here is to blow out the wire core regularly with compressed air and to replace the contact tip regularly.
Premature replacement of the contact tip
For welding jobs, especially in automated processes, there are also specifications to change the contact tip after workpiece number X. Flawless contact nozzles will certainly fall victim to this procedure and be replaced by new ones. However, the costs of interrupting the process due to a worn contact tip and the possible rework costs usually significantly exceed the costs for the necessary additional contact tip. However, there is also a bad habit among welders to change the contact tip prematurely. For example, welders have learned to change the contact tip after every break or, for example, after every fifth workpiece, to ensure that they work with flawless wear parts. Of course, this is sometimes also necessary if a highly abrasive wire is being processed, or if there is a risk of wire sticking due to strong spatter adhesion.
However, it is advisable to pay attention to visible signs of wear rather than simply assuming that the corresponding part is unusable. After all, no one wants to reduce productivity and drive up costs unnecessarily.
If a high-quality contact tip has been selected in the size suitable for the wire and the welding application, it can take a very long time until it is worn. It is not uncommon, for example, to be able to weld several spools of wire with one contact tip during manual welding.
To the point
Causes that lead to premature wear of the contact tip & first aid tips
1. Poorly adjusted process – wire sticking.
- Optimise the process parameters.
2. Poorly adjusted process – high spatter formation adhering to the front area of the contact tip.
- If the setting of the process parameters cannot be further improved, use coated contact tips that reduce adhesion, such as silver-plated contact tips.
3. Poor quality of the contact tip with poorly made inner bore and inferior material quality.
- Switch to a quality manufacturer.
4. Poor wire quality – highly abrasive wire additives. Often also due to poor surface quality.
- If the wire quality cannot be further improved, wear can be reduced with a harder contact tip material. Switch to CuCrZr or HDS.
5. The wrong contact tip was chosen, the bore diameter does not match the wire diameter.
6. The contact tip is overheated.
- Make sure to have a firm fit before starting work.
- Do the specified performance data match the welding parameters, or is the torch overloaded?
- If using a liquid cooled torch, check the cooling circuit.


Torch neck damaged by misuse
The torch neck is the component on the welding torch through which the welding wire and the shielding gas are fed into the process. At the same time, it ensures the power transmission to the contact tip and ensures that the heat is dissipated from the process as quickly as possible. Like all parts on the welding torch, the torch neck is a very robust component. Perhaps this is precisely why it is often misused as a hammer, for example to fit components during welding. Unfortunately, it is sometimes forgotten that considerable damage to the torch neck can occur, depending on the intensity of the hammering.
Depending on the torch type and manufacturer, the exterior of the torch neck is made of coated steel, stainless steel, brass or a plastic coating. There is insulation between the outer pipe and the inner live parts.
Liquid cooled torch necks are more sensitive than air cooled ones, due to their additional channels for the supply and return of the coolant. If a liquid cooled torch neck is hammered or used to hit an object, for example to knock off spatter adhesions in and on the gas nozzle, damage can occur that restricts the coolant flow and leads to overheating of the torch. Impact points and deformations on the torch neck are particularly critical here. Unlike a completely blocked coolant flow, a reduced coolant flow is not detected by the power sources and displayed as a fault. As a result, the torch is undersupplied with coolant and is no longer protected against overheating.

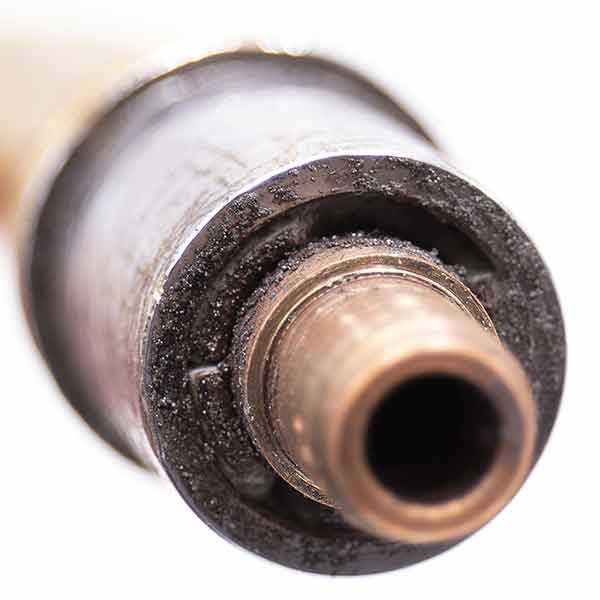
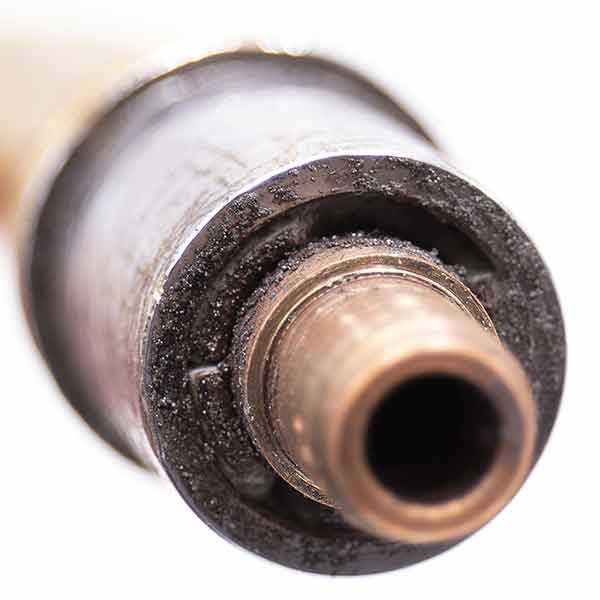
Broken insulation sleeve
Insulation sleeves
The insulation sleeve at the front end of the torch neck is one of the first components that can break in case of improper hammering or hitting of the torch neck. If this happens, a short circuit is created, which is called micro arcing within the torch neck, and can lead to hole formation. If the impact force is particularly strong, even the outer tube of the torch neck can be bent and the underlying insulation damaged, which in turn causes short circuits.
Because they are aware of the handling and misuse of torch necks, torch manufacturers offer correspondingly robust welding torches. With the so-called shipyard torches in the ABIMIG® line from ABICOR BINZEL, the outer tube is particularly resistant to harsher working and environmental conditions, as well as to slightly rougher handling of the torch neck.
Gas nozzle seat
There are welding torches with push-on and versions with screw-on gas nozzles. When push-on gas nozzles are used, it is advisable – especially if the gas nozzle is frequently changed, replaced or twisted – to look at the gas nozzle seat. Signs of wear can occur that make a change of the torch neck necessary. A sure sign that the torch neck needs to be replaced is a gas nozzle that is no longer firmly fixed in place.
O-rings
In the case of interchangeable and rotatable torch necks of liquid cooled welding torches in particular, the O-rings at the interface between handle and torch neck are components that need to be maintained. They must always be lightly greased in order to prevent shearing when the torch neck is changed, which can happen with dry O-rings.

Contact tip holder
Welding torches are available in versions with exchangeable contact tip holder and with firmly soldered contact tip holder. The advantage of a fixed contact tip holder is the better heat dissipation compared to a replaceable one, which also makes the welding torch more resilient. The disadvantage is a shorter service life of the torch neck, because each change of the contact tip also wears out the thread of the contact tip holder – which cannot be replaced. If the thread of the contact tip holder is faulty, this does not cause any problems, as long as the shoulder of the contact tip remains attached, because the current can still be transmitted over a large area. However, if this is no longer the case, the only solution is to replace the complete torch neck.

Liquid cooled welding torches
The demands on the cooling of the welding torch are also high in the high-ampere range. Depending on the torch type, the coolant in the torch neck is guided differently. Some welding torches – such as the ABIMIG® GRIP W 555 from ABICOR BINZEL – even have a dual-circuit cooling system. In general, the more complex the cooling circuit, the more complex the front structure of the torch neck.
A liquid cooled torch neck can be easily damaged by overheating. A typical trigger for this is that there is still air in the system when the welding process is started. After welding, the coolant flows back into the cooling unit from the torch neck and cable assembly over time, as is commonly known. If a completely “empty” torch starts off welding at a high amp rate, this means an enormous temperature load for the welding torch. Therefore, it is advisable to wait a few seconds before welding to ensure that the coolant has arrived at the very front of the torch neck as well.

Sometimes there is not enough coolant in the cooling unit, so the coolant level must also be checked at regular intervals. From time to time, the coolant should also be replaced due to contamination of the liquid. Particles in the coolant can settle in channels in the torch neck and thus reduce the flow.
Why only coolant, and never water, should ever be used for torch cooling, is explained in detail in chapter »Cable assembly for MIG/MAG welding torches« genau erläutert.
Air cooled welding torches
Temperature damage due to overheating usually occurs with air cooled welding torches when welding is carried out longer with higher parameters than permitted for the torch. The permissible load is usually specified for 35% or 60% duty cycles. The overload becomes visible as a result of above mentioned discoloration of the wear parts. With extreme stress due to heat, discoloration even occurs on the torch neck. For this reason, it is essential to use a welding torch suitable for the task and not to burden it beyond its technical performance limits. In case of doubt, it is better to use the next higher size torch or a suitable liquid cooled welding torch.

Everyone knows that it is a matter of pure luck to have a perfectly functioning torch after doing this, but it is still done in practice: torch necks are clamped in a vice and then bent. This is an absolute no-go! The greatest danger with such a procedure is the damage to live parts or insulation.
Good welding torch manufacturers offer special torch necks with various angles and lengths for special challenges. It makes sense to have a special torch made, especially if you weld repeatedly in a specific position. Torch necks with geometries that deviate from the standard are often required in order to be able to weld hard-to-reach areas in the required quality. Some providers already have possible special torch solutions in their standard portfolio. With the ABIMIG® line, ABICOR BINZEL offers rotatable and exchangeable and even flexible torch necks. With exchangeable torch necks, the torch neck can be replaced within a few seconds. Flexible torch necks can be individually adapted to the different requirements by the welder on site.
To the point
Causes that lead to premature wear of the welding torch neck & first aid tips
1. Misuse of the torch neck as a hammer – deformations occur that lead to an undersupply of the welding torch with coolant and, as a result, to overheating. The insulation sleeve can also break.
- Avoid misuse of the torch neck.
2. Loose fitting gas nozzle – the gas nozzle seat may be worn, due to frequent changes of the gas nozzle.
- Change the torch neck.
3. Unauthorised bending of the torch neck – live parts are damaged – greatest risk!
- Ask your torch manufacturer about curved torch necks. There are special torch necks, and even flexible torch necks, for special applications.
4. With liquid cooled torches with exchangeable necks: O-rings at the interfaces between handle and torch neck are too dry and shear off.
- Grease the O-rings when changing the torch necks.
5. Welding torch overheated – there are discolorations on the gas nozzle and/or on the torch neck.
- Use only welding torches suitable for the task. If in doubt, use a welding torch with a higher power specification.
- Reduce the duty cycle.
- With liquid cooled torches, check the cooling circuit for faults.
6. Welding torch overheated – reduced coolant flow. The coolant lines at the machine connection are buckled.
- Check the coolant level and replace dirty coolant. Electro corrosion particles settle and clog the channels. Never use water as a coolant!
7. Welding torch overheated – there is air in the cooling system.
- Before welding, give the coolant enough time to arrive at the very front of the torch neck and flow through the entire system.
- Check the lead time and lag time settings of the welding machine.

The cable assembly of a welding torch serves as a connection between the torch neck and the welding power source in order to supply the torch with electricity, gas, wire and, in the case of liquid cooled welding torches, with coolant as well. Usually the MIG/MAG cable assembly lies on the floor and is pulled during welding, pushed away, kicked away, folded, laid over and pulled over sharp edges, gets cut or is squeezed because a forklift truck drives over it … the constant strain leaves its mark. This is visible not only on the outside, but inside the cable assembly as well, cables can be squeezed or clamped by such heavy use, and break or tear off at the connection points.
The fine copper cables within the Bikox cable are damaged in the event of extreme bending or crushing of an air cooled cable assembly. A cross-section of an air cooled cable assembly illustrates this.
Inside an air cooled cable assembly, when viewed from the centre, the hose for the gas supply runs with the liner for the wire, which is then surrounded by the copper strands and the lines for the torch switch or, depending on the torch type, other additional signal lines. All these components are coated with an insulation layer. With excessive bending or squeezing, a few of the fine copper wires tear off each time, and the resistance increases. Although this is natural wear and tear, it is significantly accelerated by improper use.

Cable assembly length
It is not uncommon at welding workstations in production plants to see welding torches that are equipped with cable assemblies that are too long or too short. Cable assemblies chosen too long are not only awkward and often get in the way, they are also heavier for the welder to handle and can lead to wire feed problems.
Good welding torch manufacturers are constantly working on reducing the weight when developing their cable assemblies by using special materials. But even a lightweight cable assembly with a length of 5 metres is still heavier than the same cable assembly that is 4 metres long. A closer look at the welding task is worthwhile. Often a cable assembly length of 4 or even 3 metres is sufficient.
In addition to better manageability for the welder, the choice of the right cable assembly length also has an influence on the performance of the complete welding equipment. If the cable assembly is too long, it can easily lie in loops, wrap around table legs or other parts on the floor and complicate the wire feed. The consequence of this can be premature wear of the cables or the wire feeder.
A cable assembly that is too short also places a strain on the internal cables and the connection points – to the torch neck on one hand and to the power source on the other. If the components are constantly pulled, the control cables and the power connection at both cable assembly ends can be damaged or even ruptured. Such a tensioning effect is also caused by improper pulling on the cable assembly to move the power source to another place.
In the case of a liquid cooled welding torch, the supply and return hoses for the coolant can be torn off under tensile stress. Total failure of the welding torch is therefore preprogrammed.
Therefore, the cable assembly must not be chosen too short or too long.

Source of danger from damaged cable assembly
Proper storage of a cable assembly
MIG/MAG welders are not exactly gentle with their equipment. This is precisely why it is important to sensitise welders to their work tool, the welding torch. Careful handling is vital in order to maintain the functionality of a cable assembly for as long as possible. This includes protecting the cable assembly from falling parts as well as from being run over by forklifts and the like, from squeezing or buckling due to carelessly discarded parts and much more.
Excessive buckling should be avoided at all costs if the cable assembly is placed down before the welding process. Any buckling and every additional loop prevents a smooth wire feed, which is a basic requirement for a smoothly running welding process.

A protective hose as additional protection is not as much in demand and common in Germany or Europe as it is in comparison on the American market or in the Middle East. There are different types of cable assembly protective hoses, which can be made of different materials, such as leather or Kevlar. When used correctly, they can significantly extend the service life of the cable assembly.
Of course, an additional protective hose also means more weight and greater stiffness of the cable assembly. On the other hand, it means longer protection, which is especially useful where external stress cannot be avoided.
Protective hoses made of leather are also used in welding fume extraction torches. This is also the case with the RAB GRIP, RAB GRIP HE 2, xFUME® PRO and xFUME® COMPACT from ABICOR BINZEL, which are all equipped with leather protective hoses as standard over approx. 2/3 of the total hose length. This attaches directly to the buckling protection and prevents the extraction hose from getting stuck or being cut if it is pulled over sharp edges.
The maintenance of the coolant is a topic that is unfortunately often neglected in the maintenance of a welding torch. What is not taken into consideration: coolant also ages. Some operating instructions recommend replacing the coolant once a year. However, if a welding torch is in regular use for a long time, the recommended conductivity (unit = Siemens per meter or microsiemens per centimetre) may already be exceeded with a one-year cycle.
On average, it is recommended to check the conductivity of the coolant between once a month and once a quarter, depending on the frequency of use and the duty cycle of the torch. For each welding process, there are conductance values that require the coolant to be replaced. These are:
- MIG/MAG: over 350 µS/cm
- TIG: over 250 µS/cm
- Plasma: over 30 µS/cm
The market offers measuring instruments for measuring coolant conductivity. One of them is the Primo 5 from Hanna Instruments, which is also offered by ABICOR BINZEL. For the conductivity test, the meter is simply immersed in the coolant filler neck on the cooling unit or power source. The result can then be read on the display of the measuring device. Please also remember to calibrate the measuring instrument regularly.
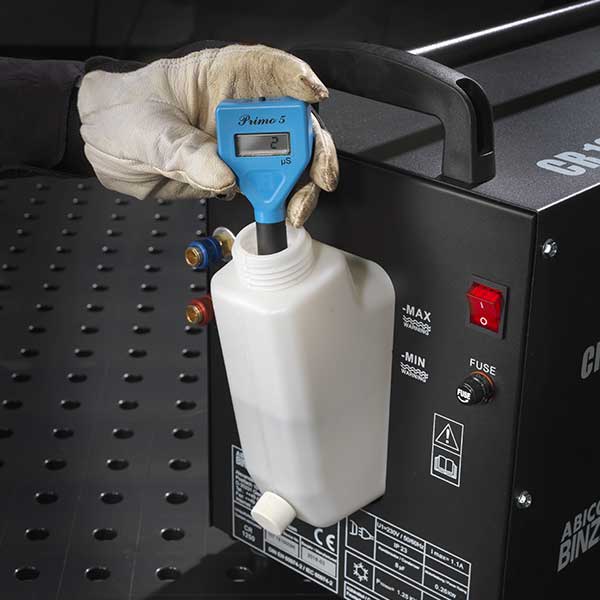
Determination of the conductivity with the Primo 5
Why not water as a coolant for welding torches?
Depending on its source, water has different conductivities for the transmission of electricity. Ultrapure water has practically no conductivity because it contains virtually no foreign substances that make water conductive in the first place. Substances dissolved in water, such as chlorides, sulphates and carbonates, thus make tap water an excellent electrical conductor. If, for example, tap water is used as a coolant for a welding torch and electricity flows through the water in the torch system, a chemical reaction occurs. The cooling circuit of a welding torch uses many different materials with different electrochemical potentials that react under the influence of water: “less noble” materials such as brass dissolve and become more “noble” materials such as e.g. copper. In this way, the smallest components of live cables, connections, cooling cables, etc. are detached and settle in the welding torch with the result that the torch fails.
However, tap water as a coolant in a welding torch system not only destroys the torch. The power source and all other parts involved are also exposed to the decomposition process. Water as a coolant is therefore by no means recommended!
More information you can also find in our blog article »3 reasons for not using water as a coolant for welding«
To the point
Causes that lead to premature wear of the cable assembly & first aid tips
1. Bending or pulling the cable assembly sharply – fine copper wires tear and increase the electrical resistance of the current conduction. Control cables on the ends of the cable assembly, as well as the power connection, can be damaged.
- Make sure that the cable assembly is placed down loosely.
- Choose an optimal cable assembly length.
- Avoid pulling and tugging, and do not move the power source using the cable assembly.
2. Cable assembly is squeezed or bent off – smooth wire feed is not guaranteed.
- Place the cable assembly carefully down outside other areas of activity.
3. With liquid cooled torches, overheating of the cable assembly – wire feeding hose or sheathing of the power cable show heat damage or reduced coolant flow, coolant lines at the machine connection are bent.
- Check the coolant level and replace dirty coolant. Electro corrosion particles settle and clog the channels. Never use water as a coolant!
4. Check the coolant level and replace dirty coolant. Electro corrosion particles settle and clog the channels. Never use water as a coolant!
- Before welding, give the coolant enough time to arrive at the very front of the torch neck and flow through the entire system.
- Check the lead time and lag time setting on the welding machine.

The task of the liner is to pick up the wire from the wire feeder and to guide it evenly and with as little friction as possible through the cable assembly and the torch neck to the contact tip, and from there into the process. All MIG/MAG welding torches have such a wire feed system. The liner – other terms used are wire liner, neck liner or wire feeder liner – is a wear part.
In wire liners and wire feeder liners, the guide element is generally a steel liner. A neck liner means the part of the wire feeder through the torch neck, which is used, for example, in rotatable and exchangeable torch necks. A neck liner is usually a pure metal liner, because this part is directly at the process and has to withstand great heat. Plastic liners are comparatively smooth and flexible at the same time, which ensures a low friction wire feed. Combined liners are used because of their combination of plastic liner and attached brass liner, and the resulting good wire feed and high heat resistance at the end of the torch head.
Each wire has its own special features and is individually friction intensive. This means that you need to have a good knowledge of the characteristics of the wires you want to weld with in order to be able to choose the right liner.
Characteristics of different welding wires
The table below shows the characteristics of the most common welding wires:
Wire type | Friction intensity |
---|---|
Bare wires | Less friction-intensive |
Copperplated wires | Less to medium friction-intensive |
Aluminum wires | Highly friction-intensive |
CuSi wires | Highly friction-intensive |
Filler wires | Highly to extremely friction-intensive, depending on the folding and surface |
The wire material itself is an influencing factor on the friction intensity. The degree of purity of the production with possible residues from drawing soap and the like plays a no less important role. If these are brought into the process, this will have an impact on the quality of the weld seam. Contact your wire supplier directly if you repeatedly encounter problems with the degree of purity of the wire.
In order to avoid wire feed problems, the selected liner must match the material surface of the wire. In addition, the liner must be able to withstand the high thermal loads during welding without changing its structure and properties. The right size ratio of welding wire to the diameter of the liner is also an essential point that must be observed. Up to 95 percent of problems with the wire feeder are due to the incorrect diameter of the liner being used.

You should be aware of their individual characteristics when choosing a liner. The most important characteristics are compiled below:
Bare steel liner
The surface of this liner is made corrosion resistant by means of phosphating and it is polished in addition. This processing is called bonderising and it makes the bare liner highly robust. It is suitable for low friction SG steel wires, copper-plated and non-copperplated, and for use in all liquid cooled manual welding torches. This liner is generally not suitable for use in air cooled welding torches.
Insulated steel liner
This versatile liner consists of a bonderised (phosphatised) spring steel – i. e. a special protection against corrosion – which is coated with plastic insulation in blue, red or yellow. It can be used in all air cooled and liquid cooled MIG/MAG welding torches, with and without a separate wire feeder, for wire thicknesses up to 2.4 mm. Also for MIG/MAG robot welding torches. It is also suitable for SG steel wires, both copper-plated and non-copper-plated.
Insulated steel liner BSL
These liner types, which are also made of CrNi blank bonderised spring steel, are specially designed for use in robot welding torches, and offer a fine size gradation in the colours pink, blue, black, grey, white or red. They are suitable for feeding copper-plated and non-copper-plated steel wire, as well as stainless steel wire, in standard MIG/MAG welding and impulse welding with robot welding torches.
PTFE plastic liners
This Teflon® plastic liner is ideal for stainless steel because it has excellent sliding properties. It comes in the colours blue, red or yellow, is heat resistant up to a maximum of 260°C and is also suitable for welding standard stainless steel wires and CuSi wires. When stainless steel wire is welded, it is essential that carbon steel – the abrasion of a wire core – does not get into the weld pool and contaminate the process.
Carbon PTFE plastic liners
This Teflon® liner has graphite as a bonded lubricant and has very good sliding properties with its carbon content of up to 20%, because the surface is friction minimised. The colour code is grey-black and it is used in manual MIG/MAG welding torches, both air and liquid cooled. Owing to its good sliding properties, this liner feeds aluminum wires and welding wires with special alloys extremely well.
BPL plastic liners
These are regarded as the jokers for welding aluminum wire, wires with special alloys, cored wire and stainless steel wire. This liner, made of plastic with the PTFE fluorine/ compound PPS O2 (semi-crystalline polyphenylene sulphide), with its ceramic additive and a stainless steel inlet tip, provides excellent sliding properties and is often used when problems arise with other liners. It is heat stable up to 260°C and can be used with all air and liquid cooled MIG/MAG manual torches for wire thicknesses up to 1.6 mm. Colour codes are orange and petrol.
PA plastic liner
Its low thermal stability of only up to a maximum of 65°C allows this polyamide liner to be used exclusively as a combined liner – ideally in combination with a brass liner, the length of which should be kept as short as possible in order not to reduce the very good sliding properties of its high surface hardness. A critical thermal load is thus counteracted. This PA liner can be used for all welding wires in air cooled and liquid cooled MIG/MAG welding – even in the CMT™ (cold metal transfer) process from Fronius® or comparable processes from other manufacturers.
PA combination plastic liner
With this polyamide plastic liner with a brass liner attachment, the good sliding properties of the PA liner come together with the thermal stability of the brass liner. This plastic core is mainly used in liquid cooled MIG/MAG manual welding torches and is used for steel wires, stainless steel wires and filler wires or as wire feed for the TIG cold wire system.
The length of time that liners can be in use depends on many factors. These start with the choice of the right liner for the welding wire used and go all the way to the drive rollers that transport the wire into the process. In the following you will find out which measures can be taken to prevent premature wear of liners and what may be the cause of and solution for occurring wire feeder problems.
The most common reasons for the premature failure of wire feeder systems are:
- Wire sticking
- Non-deburred edges when cutting
- Incorrect contact pressure of the drive rollers
- Using the wrong wire core
- Wrong size of liner
- Poor wire quality with rough surface or dirt
The standard welding errors undoubtedly include wire sticking. This is caused by the wire burning on inside or at the contact tip and making further wire feeding impossible. Causes and solutions for this can be:
The wire has too much slip in the wire feed and runs irregularly
The pressure rollers must be tightened. With each feed, the pressure of the wire feeding rolls can be easily adjusted.
Too much friction in the wire feeder due to cable assembly being too long
If the cable assembly is very long, the use of a push-pull welding torch helps. The wire is pulled further, and can thus be fed at a uniform speed, with the help of a motor installed in the torch body.
Unnecessarily high frictional resistance due to wrong liner
The characteristics of different liners are explained directly before this subchapter and provide a good help for a correct preselection.
The entire welding torch is insufficiently cooled, the contact tip is thermally overloaded. There can be several causes for this:
- The coolant level is too low and needs to be topped up
- The coolant flow is partially blocked and needs maintenance
- The cable assembly is bent and must be placed more loosely
- The general wear condition of the welding torch is too high, the torch needs maintenance
- The torch is overloaded and a more powerful torch must be used for the welding parameters
- The wrong contact tip was used
- If none of these causes apply, talk to your welding specialist. Other factors can come into question in case of a thermal overload of the contact tip and these must be considered individually.

The wire feeder is not continuous because the liner was cut off too short and is not flush with the contact tip
When the contact tip is screwed on, there should be a slight pressure on the liner, then it is flush. Counter-pressure is achieved through the union nut on the central connection.
With a straight torch neck there is only a poor contact to the contact tip, micro arcs can occur and the wire burns on
When using straight torch necks in combination with wires with a low dressage – i. e. a low pre-bending of the wire due to e.g. winding on wire spools or in drums – the contact point in the contact tip can change. This leads to an uneven welding process and micro arcs are created, which can lead to sticking.
A torch neck with a slight bend allows so-called pre-dressage of the wire, which then fits evenly in the contact tip and contacts better. The wire is also pre-skin passed (preprocessed) by tightening the wire feeding rolls more firmly.
Too many unwanted short circuits lead to excessive weld spatter formation
It is very likely that the welding parameters are not optimally set. They must be checked in order to avoid transition arcs as far as possible.
Each individual part on a MIG welding torch has connection points. The wire feeder is no exception. Any connector through which the welding wire is conveyed represents a potential hazard point.
When changing a torch neck, care must always be taken to ensure that the connectors are attached stably, firmly and without burrs. The main liner, or the liner through the cable assembly, must be connected to the wire liner of the torch neck without hindrance. Check that there is no gap between the main liner and the neck liner.

As with many things, the topic of cleanliness also plays an essential role for the liner and the welding wire. Blowing out the liner with compressed air is usually only necessary if the surface of the wire, the wire spool or the wire drum are not kept clean. Here, the use of a cleaning fleece provides the first remedy. Other simple measures at the end of a working day, such as using a plastic cover for the wire roller, can also have a significant impact on the functionality of the wire feeder and prevent it from clogging up with dirt particles or wearing out prematurely.
For particularly sensitive welding wire, it is recommended to peel off the wire spool at the end of the work and place it in a closed container or area, to prevent dust or moisture from accumulating on the wire and causing rust to form.

When cutting the liner to size, a common mistake is failing to debur the edges created during cutting. Each burr is an obstacle to the wire and impairs a low-friction wire supply. In the worst case, the wire “builds up” and leads to a failure of the system. Use a sharp side cutter to create the cleanest possible cutting edge when cutting.
When cutting the wire, always make sure that there are no burrs or sharp edges pointing inwards and impairing or hindering the wire feed. This applies to both the connection side to the machine and the torch head side to the contact tip.
If the liner is cut off too short, so-called micro arcing – unwanted arc formation – can occur in the liner due to the resulting gap. This can also lead to the failure of the liner.

Each welding wire from a drum or wound onto a spool has a twist or pre-dressage. This winding usually forces the wire to return to the original shape it had in the drum or spool. As a result, the welding wire never runs absolutely straight into the wire feeder and rubs on the inside of the liner. In this case, the smallest grated particles of the wire can get into the wire feeder and clog it. As soon as this happens, the only thing to do is to change the liner.
A straight wire can be inserted most easily and without major friction into a liner and thus also into the contact tip. In order to increase the service life of the liner and also the service life of the contact tip, a wire straightener can be attached to the rear end of the wire feeder before the welding wire enters the actual feeder. These devices are not absolutely necessary, but they can help to avoid premature wear of the liner.
The drive rollers or wire feeding rolls must not be ignored when the liner is being serviced. In order to prevent problems with the wire feed, one thing applies above all to drive rollers: wire feeding rolls and welding consumable material must match in terms of size and type.
Different wires require different drive rollers. As a rule, there are two grooves for different wire diameters on a wire feeding roll. If the diameter of the wire to be welded changes, the wire feeding roll is simply turned in the unit. The grooves are V-shaped (V groove) for steel wire, U-shaped (U-groove) for aluminum wire, or have a so-called perforated U shape for cored wire. There is no one-size-fits-all or at least uniformly standardised specifications for wire feeding rolls. This explains the wide variety of greatly different designs with regard to the material of the rollers, their quality, as well as the diameter and width of the grooves.

A U-groove is used for welding aluminum wire, because this does not leave any unwanted deformations of the soft aluminum. With this wire material, the contact pressure also plays an important role. If it is too high, softer welding wire is quickly deformed. But even harder welding wire can be transformed into square or oval wire due to incorrectly adjusted contact pressure, which can prematurely wear out other components of the welding torch when fed through the liner up to the contact tip, or even cause damage to the liner. Too low contact pressure, on the other hand, means that the wire is not fed reliably to the welding process.
Very thin, sensitive aluminum wires are best welded with a socalled push-pull welding torch, which is equipped with a carbon PTFE liner. Here, the welding torch with integrated motor in the torch body takes over the additional pulling of the welding wire. Of course, the prerequisite must be that the welding machine with its wire feed drive and the PP torch are optimally matched to each other.
The bottom line is that every manufacturer of MIG/MAG welding machines has already installed the right wire feeding rolls for their devices and their application portfolio in their units. If you have special applications, your wire supplier or welding torch manufacturer will also be happy to support you.
If there is any uncertainty as to whether the wire feed is still intact, a mechanical tensile test will help.
This is carried out as follows:
- Loosen or release the wire feeding rolls
- Place welding torches on a level, or only minimally angled if possible
- Pull the wire by hand through the welding torch
The following rule applies here: if the wire cannot be pulled through by hand, both the welding wire and the liners must be checked.
The aim should always be the lowest possible force that is required for pulling through. However, the correct range for an application varies greatly, because several factors play a role, such as different wire types, the length of the welding torch or the diameter of the wire.
To the point
Causes that lead to problems with the wire feed and premature wear of the wire liner & first aid tips
1. Uneven wire feed – wire has too much slip.
- Adjust the pressure of the wire feeding rolls.
- Check that wire feeding rolls match the wire installed.
2. Uneven wire feed – incorrect inner diameter of the wire liner.
- Check that the wire liner matches the wire diameter.
3. Uneven wire feed – very high frictional resistance.
- Use only liners that match the wire. To do this, use the table in this chapter.
4. Uneven wire feed – abrasion particles are clogging the liner.
- Clean the liner with compressed air. Use a cleaning fleece.
5. Uneven wire feed – cable assembly is too long.
- Avoid unnecessarily long cable assemblies, which are probably also laid in narrow radii as well.
- Use a torch neck with a lower bending angle to reduce friction.
- Check whether a wire with better quality can be used.
- Use a push-pull welding torch if a long cable assembly is needed in conjunction with a wire that is hard to feed.
6. Uneven wire feed – the wire feeder is not continuous and is not flush with the contact tip.
- Make sure you feel a slight pressure on the liner when screwing in the contact tip.
7. The liner wears out excessively fast – the liner being used does not match the wire.
- Choose the right material for the welding wire or combination material of the liner. To do this, use the table in this chapter.
8. The liner wears out excessively fast – wire has no pre-dressage creates too much friction in the liner.
- Attach a wire straightener at the rear end of the wire feeder.
9. Wire “builds up”, so-called “nest formation” – burr at the end of the wire gets stuck.
- When cutting the wire, always deburr the edges.
10. Wire “builds up”, so-called “nest formation” – incorrect inner diameter of the wire liner.
- Check if the wire liner matches the wire diameter.
11. Wire “builds up”, so-called “nest formation” – the wire feeder is not continuous and is not flush with the contact tip.
- Make sure you feel a slight pressure on the liner when screwing in the contact tip.
- Use a push-pull welding torch if a long cable assembly is needed in conjunction with a hard-to-feed wire.
12. Wire “builds up”, so-called “nest formation” – frictional resistance is too high.
- Abrasion particles are clogging the liner. Clean the liner with compressed air. Use a cleaning fleece.
13. Wire “builds up”, so-called “nest formation” – cable assembly is too long.
- Avoid unnecessarily long cable assemblies, which are probably also laid in narrow radii as well.
- Use a torch neck with a lower bending angle to reduce friction.
- Check if a wire with better quality can be used.
- Use a push-pull welding torch if a long cable assembly is needed in conjunction with a hard-to-feed wire.
The machine-side connection – also known as the central socket and central plug – is the connection from the power source to the cable assembly and is responsible for supplying electricity, gas and welding wire. The signal lines of the torch button are passed through the machine connection in the EURO central connection. In the case of liquid cooled torches, the coolant is fed and returned via two quick connectors, into which the coolant lines of the welding torch are inserted. Machine-side connections and control cables are among the less maintenance intensive components of MIG/MAG welding torches. Only individual components such as the O-rings and connection plugs of the control cables have to be checked regularly and, in rare cases, serviced. It is very important to pay attention at all times to a firm fit of the electric contact connections.

The O-rings of the central connection are wear parts. There are different connections and a different number of built-in O-rings, depending on the welding power source. The majority of the devices have an EURO central connection with an O-ring on the gas connection. Its task is to seal the connection of the gas supply and to direct the gas flow into the gas hose of the welding torch without leakage.
O-rings can wear out, depending on how often a complete torch is removed from the welding machine. If this is done every day, the O-rings should be regularly treated with grease and thus kept supple, which reduces early wear due to drying and tearing. Defective O-rings mean a leaking gas supply. Welders compensate for this by simply increasing the gas supply. With this method, too much gas is wasted and production is therefore more expensive. By maintaining a small wear part you can prevent unnecessary gas costs, as well as unintentionally higher gas consumption, and at the same time protect the environment. If the welding torch is removed rather infrequently or irregularly, there will be hardly any problems with the machine-side connection. Checking the O-rings before connecting the torch is recommended.

The torch must be removed from the machine for maintenance work, such as changing or blowing out the liner. When reconnecting, it is important that the central connection is securely tightened. If the machine-side connection is a Euro central connection, the coupling nut must be tightened firmly. Other types of connections often use a power contact pin, which of course must also have a firm fit when connected. If, for example, the wire feeder is changed, this current contact pin must also be removed. Because these pins are not moving parts, they cannot detach on their own – unless they are only loosely connected or forcibly removed.
If the central connector is not firmly connected to the power source, the most common errors that occur are:
- High resistance
- Power transmission failure
- Arc formation on the machine-side connection
Such loose connections usually arise when in a hurry the welder neglects to tighten the union nut or the terminal of the power contact pin. Among other things, there is a risk of damaging the torch or the wire feed connection. Downtime and costs can skyrocket due to this small omission.

An additional control cable is used for signal transmission, depending on the type of central connection, or if the torch is equipped with a module for remote control of the welding power source. Like other connecting parts, the control cables must also be tightly connected. A common mistake here is to simply insert the control cable plug, without rotating the fastening ring in its lock to create a firm connection. A possible loose contact is the result. Conversely, when removing the control cable plug, care must be taken to loosen the locking ring. In some cases, the welding torch is disconnected from the central connection without first loosening the control cable plug. This can tear out the cable or damage the contacts.
Since each welding system differs in its design, ABICOR BINZEL designed a common industry standard for connection systems of air cooled and liquid cooled MIG/MAG welding systems more than 40 years ago: a central socket and central plug from ABICOR BINZEL, usually called a EURO central connection. With over 500 different central socket types listed, you are sure to find the right socket for your machine type in order to switch to this uniform torch connection.
To the point
Causes that lead to premature wear of the machine-side connection and control cable & first aid tips
1. Leakage in the gas flow – O-ring is defective, porous, torn.
- Check and grease O-rings regularly before connecting the torch.
2. Power transmission failure – central plug is not firmly connected to the power source, resistance increases.
- Make sure that the central connection is securely connected by tightening the union nut firmly.
- Check the secure connection of contact pins, as well. Never remove them by force when changing the wire feeder but remove them properly.
3. Arc formation on the machine-side connection – connection of the terminal or the current contact pin is too loose.
- Make sure that the central connection is securely connected by tightening the union nut firmly.
4. Disturbed signal transmission of the control cable – control cable plug is only plugged in.
- Rotate the mounting ring of the control cable connector in its lock to create a firm connection. Loosen the mounting ring when the central connection is removed.
Editorial team
We hope that in this e-book you have been able to find a lot of valuable information and tips for the correct handling and maintenance of your MIG/MAG welding torches. If your equipment is properly maintained, nothing stands in the way of productive work, good welding results and enjoyment of your the MIG/MAG welding torches for a long time.
Your suggestions and comments on this e-book are welcome.
The following contributed to the creation of this e-book:
ABICOR BINZEL, Germany
Boris Rinn, Product Manager MIG/MAG Manual Products
Prof. Dr.-Ing. Emil Schubert, Technical Director CTO
Herbert Burbach, Art Director
Carmen Laux, Marketing
Christine Rinn, Marketing
Stefan Schneider, Marketing