Spool welding robot SWR: faster and more efficient pipe welding
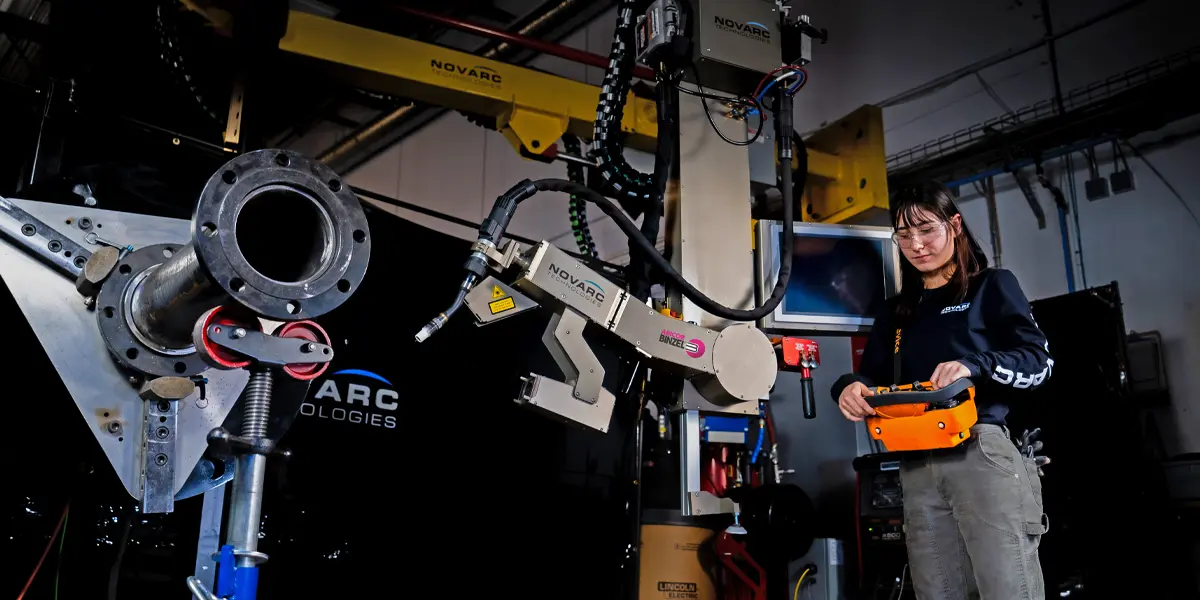
Increase productivity in pipe welding with this collaborative welding robot
If you are looking for a way to organise your pipe processing more economically, we have the solution for you: the Spool Welding Robot, SWR. Depending on the welding job, you can use this collaborative robot to weld steel pipes with a wall thickness of up to 50 mm just as well and precisely as stainless steel pipes with a wall thickness of 2.5 mm or more – and you can weld non-stop from the root to the cap layer.
Thanks to the intuitive operation and the inclusion of up to 60 pre-programmed weld recipes, it is very easy for you to adapt the spool welding robot into your workshop. With the use of Novarc’s NovEye™ visual camera system you can easily reduce your reliance on highly skilled welders while significantly increasing your productivity in pipe welding and reducing your repair rates with x-ray quality welds.
Welding black steel, low-alloy steels, stainless steel or nickel alloys faster in pipe processing and reducing costs at the same time has never been so easy. Take advantage of the great potential for maximising your profits in pipe welding offered by the SWR spool welding robot. This turnkey system solution is made possible by the international co-operation between Novarc Technologies and ABICOR BINZEL.
Equipment of the SWR
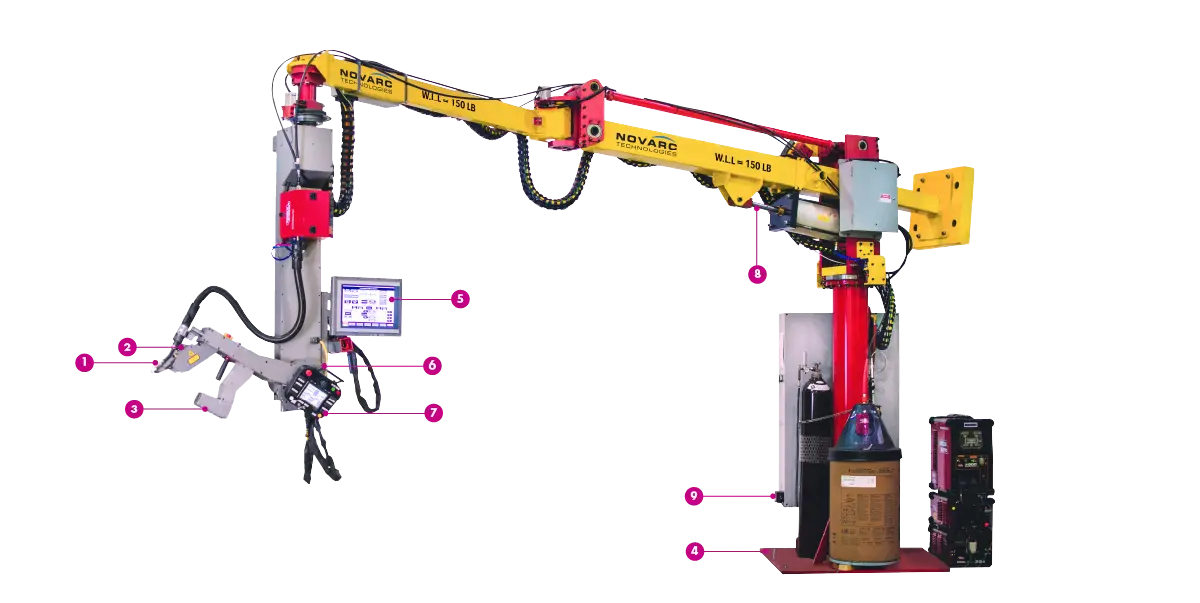
- ABIROB® W robot welding torch
Slim design and compact torch head ensure good access to the welding joint. - Height adjustment laser
Maintains the working height to the workpiece in the event of out-of-roundness pipes. - NovEye™ vision system
Records every weld in real time and provides enhanced view of the weld groove, weld pool, and wire stick out helping to improve weld quality as well as providing accountability and traceability for your QA/QC Managers. - Small footprint
The 330° workspace of the SWR offers maximum accessibility within your production area. The SWR base plate footprint only takes up 2.5 m² of your production area floor. - Human Machine Interface (HMI) screen
Easy to use HMI for selecting the pre-programmed welding procedure and fine-tuning the welding parameters. These basic parameters (material, diameter, wall thickness, number of layers) allow a quick change of programmes and components. - 3-axis robot arm
Enables all required movement needed for roll welding with smooth torch movement for up/down, left/right, while creating weave motion.
Optional: 4th axis designed for flange welding – SWR-F
SWR-F expands on the standard SWR capability by allowing the arm to get in the optimal position of fillet welding on rotating pipes. Flanges come in several varieties and require multi-pass fillet welds on both the inside and outside of the flange, where it meets the pipe. SWR-F is capable of welding these multi-pass welds from start to finish without the need to stop between passes or re-position. - Wireless teach pendant
Equipped with toggle switches, pushbuttons and joystick for easy operation of start, stop and online changes to the movement and welding parameters. - Pneumatic height and lateral adjustment
Easy to use manipulator with a radius of 4.5 m, suitable for pipes ranging from 2" (5 cm) to 60" (152 cm) in diameter. A longer boom arm option is also available that is suitable for welding pipe spools up to 12 meters in length. - Gas management system EWR 2 Net
Reduces your carbon footprint while saving shielding gas and optimising shielding gas coverage during welding, incl. data recording of shielding gas consumption per weld.
Proven technology for pipe welding
User-friendly
The SWR can be integrated with up to five welding positioners with one SWR spool welding robot. This allows you to maximise the arc-on time while minimising the arc-off time. With this advantage you can weld on one pipe, as the other positioners are being prepared with the next pipe spool that is ready for welding.
In conjunction with the integrated laser system, the Novarc Weld Vision System can measure tolerances from the root gap and define special offset deviations. This system therefore runs continuously during the welding process. If you want to retrace the parameters and arc progression of the weld seams at a later date, you can call up the data retrospectively: on the one hand in the form of a Windows-based database table, and on the other in the form of a video that records the welding process for each weld.
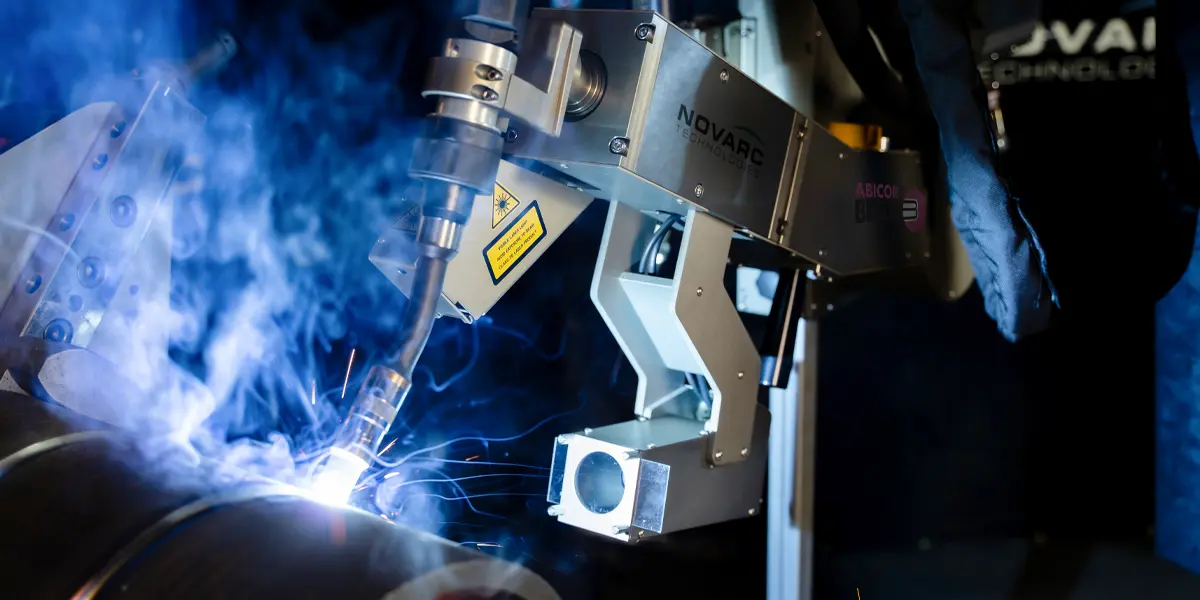
The operator can use the remote panel (wireless teach pendant) to make height and side corrections during the welding process. Even process parameters such as welding speed, current, voltage and special root processes can be directly influenced in this way. Just the way you would do it with manual welding.
Customised
Despite coming pre-programmed with over 60 possible weld programmes, the spool welding robot SWR also offers the possibility to store new programs upon request. For example: if the parameters are changed during welding these can be saved and recalled at any later date. There is also no programming experience required to operate the Spool Welding Robot.
Highly flexible
Its flexible technology is able to weld a large number of pipe connections with comparatively little space requirement. You can position the SWR on a wall, in a corner or in the centre of your production area to achieve maximum efficiency - whatever your space situation allows.
With this cobot for pipe welding, you are highly flexible and can even weld different geometries and fittings, such as:
- Pipe-pipe connections
- Pipe-flange
- Pipe bends/elbows
- Cones or truncated cones
- T-pieces
- Fittings with flange
Efficient
The SWR welds three to five times faster on carbon steel, and up to 12 times faster on stainless steel when compared to manual welding whilst delivering consistent x-ray quality welds. If you use several positioners, you can even work in parallel and, for example, remove components or reload a positioner while the SWR is welding. Changing stations or positions between positioners and components can be carried out within 3 minutes using pre-programmed welding recipes. This allows you to stop welding on one component and move to the next component when approaching interpass temperatures maximising arc on time.
This results in an almost 100 percent arc-on time per shift. Ancillary costs are therefore reduced while allowing you to increase your productivity.
Equipped with ABICOR BINZEL products
With the SWR you get an excellent combination of a cobot for pipe welding and ABICOR BINZEL welding technology products. This provides you with the best basis for consistent quality and good results when welding pipes. The ABICOR BINZEL products are as below:
There are practically no restrictions when it comes to further equipping your SWR spool welding cobot. This highly flexible system can be extended as required. Especially with solutions for the extraction at source of welding fumes during pipe welding from ABICOR BINZEL. Let's talk!
Advantages of the SWR spool welding robot
- Welds pipes from root cap without interruption
- Reduces the workload of manual welders
- Reduces dependence on highly skilled welders, whose availability on the labour market has been in sharp decline for years
- Increases productivity by a factor of 12 for stainless steel pipe welding and by a factor of 3-5 for carbon steel pipe welding
- Reduced repair rate to <1 %
- Small footprint of 1.2 m x 1.2 m
- Up to 5 welding positioners of various turning capacities can be connected in the work area
- Flexible equipment options offer solutions for any application, no matter how challenging
- Optional second weld head for high deposition welding utilising twin-wire welding technology
The challenges of pipe welding
As in any manufacturing company, the motto "time is money" also applies to pipe welding. The smarter you automate, the more economically you can produce.
You are probably familiar with the following or similar situations:
- You have to reject large projects because you don't have the capacity for additional quantities
- The setup for a welding job takes a lot of time
- Conventional 6-axis robots are not suitable for pipe welding because they are too complex to programme or block your workspace due to the necessary housing
- Fixed welding robots on rails severely restrict production and are too expensive
- If many joints have to be welded, the space required is very large
The spool welding robot SWR solves all these challenges at once. The best thing is that, depending on the frequency of use, the investment in a spool welding robot SWR pays for itself within an average of 6-18 months.
Please feel free to contact us for more information and pricing.
We also have financing options available!
Use the SWR to present interesting offers to your customers and at the same time reduce your costs and win more projects.
Technical data
Pipe diameters: | 2" to 60" |
Materials welded: | Carbon and low alloy steels Stainless and nickel alloys |
Working radius: | 15 ft |
SWR Footprint: | 4' x 4' |
Manipulator height: | 15 ft |
Manipulator working height: | 1 – 9 ft |
HMI-Screen: | 15" touch (analog resistive) |
Horizontal seam tracking accuracy: | +/- 0.1 mm |
Vertical distance control accuracy: | +/- 0.1 mm |
Weave stroke: | 0.59“ |
Weave frequency: | 0 – 5 Hz |
Weave dwell: | 0 – 0.4 sec. |
Wire diameter: | 0.035 – 0.062 in Solid, metal cored & flux cored |
Wire speed: | 30 – 1200 in/min |
FAQs:
Whether or not to use a collaborative Spool Welding Robot in pipe production surely brings up many questions. To make things easier for you and get answers right away, we have collected the 22 most frequently asked questions on the collaborative Spool Welding Robot. We hope, these will help you in the first instance.
Safety
The Spool Welding Robot meets all the safety requirements of ISO15066; therefore, the installation of a housing or safety curtains is not required.
Ratio of reach
Compared to industrial spool welding robots, the SWR has the largest ratio of reach to footprint. E. g. your shop’s footprint is limited to 2,23 m². In that case, the SWR still has a range of 4.5 m (radial) for a maximum pipe diameter of approx.1.5 m (depending on the positioner configuration).
Ergonomics
The SWR improves the ergonomics of pipe welders. It brings the welder out of rigid position while welding and takes over the weave motion. It strains off the welder‘s back and shoulder joints.
Data logging and reporting
NovData logging software allows analysis and reporting of your weld data. All welding data are stored and available for you. These data are for example heat input, positioner speed, wire feed speed, etc.
Monitoring
Each weld is stored by the NovEye monitoring system. That allows your employees to analyze and improve their process for the next welds.
Seam tracking & distance control
The SWR assists the operator in torch to pipe distance by using a laser camera and closed loop control system. With this, the operator is automatically assisted in seam tracking and can primarily keep his focus on the weld.
Collaborative robots – cobots – are industrial installations which can safely collaborate with operators in a production line. They do not require knowledge about robot programming or special programming language. They are very easy to operate and can partly be moved by hand.
Universal Robots, Fanuc, Yaskawa and others are manufacturers for six-axis Cobots on the market today.
With the base model of the SWR you can weld pipes of standard wall thickness, meaning Schedule 40 and Schedule 80 pipes. In case you need to weld pipes in your pipe processing outside these spectra, tell us about your application and we are happy to help you.
The main welding processes are: gas metal arc welding, flux-cored arc welding and metal-cored arc welding. On root we use modified short-circuit (STT, RMD, LSC). For modified waveform pulse processes we use solid wire and flux core or metal-cored wire for fill and cap passes.
With the Spool Welding Robot you can weld mild steel, stainless steel and special alloys in pipe processing.
Yes, you can. You will get quality welds with almost any standard pipe positioner to work with the SWR in your pipe production.
Taking the industry standards into consideration, the SWR falls under mechanized welding – when the operator interacts with the machine.
The Spool Welding Robot has a 1.2 x 1.2 m footprint. With this small space the SWR does not block traffic in the shop floor and it does not interfere with shop cranes. Its arm and boom can be extended and retracted to accommodate activity on the pipe production floor.
The SWR pipe welding robot increases productivity in pipe production thanks to its flexible functionality. It can integrate up to five positioners and thus enables »overlapping« cycle times and parallel work. That means: while the collaborative robot is welding on a pipe, finished components are taken off and the positioner is equipped again. The change between position or workstation is also partially automated. In this way, work cycles in the interpass temperatures can be maintained. This results in an almost 100 percent arc-on time during a shift in pipe processing and thus a significant reduction in incidental costs. As a result, productivity can be increased up to three times, which in turn increases the capacity of a pipe production many times over.
Torch hand control goes over to the SWR and with that relieves welder’s fatigue. The Spool Welding Robot has a higher deposition rate, higher production and faster track speeds. Above that, it has the ability to run pre-programmed welds.
Yes, it is easily possible. The Spool Welding Robot SWR fits in pipe fabrication shops very easily because its height does not interfere with overhead cranes. And if you want shop traffic to pass, just park the SWR away.
Installation takes two days and only one more to commission according our conditions.
An operator can be trained within 2-3 days, then he/she can do operations and maintenance.
The operator should already have some basic welding experience.
When you order the SWR, you will also get the NovData™ production monitoring software along with it. That software produces daily reports, which includes the following information:
- Production time
- Welding time
- Pipe diameter
You also get a time-stamped log file with:
- Voltage
- Weld current
- Wire feed speed
- Travel speed
- As well as other relevant weld parameters and motion parameters for each weld
The Spool Welding Robot also has a built-in camera, mounted into its robotic arm. This allows the operator to get a clear view from inside the groove on the HMI in real time. And to have data for future analysis, NovEyeä records all videos.
The shielding gas used depends on the weld process and filler metal.
The Surface Tension Transfer (STT) is highly tolerant of pipe prep variations. The Spool Welding Robot requires no more than 3mm hi-lo in pipes, even less.
The SWR needs 3 phase power and a minimum of 5,5 bar compressed air. The required electrical power can be any of the standard voltages between 208V and 600V.
The Spool Welding Robot has built-in systems to monitor speed and torque. These ensure speed and forces within required levels at all times.
The Spool Welding Robot is a robust machine. Therefore, only minimal maintenance is required. When you get operator training, maintenance training is also included.
The Spool Welding Robot needs to be anchored to a minimum 15 cm concrete slab. With overhead cranes you can move it between previously installed base locations.
The SWR can be used outside the pipe shop as long as it is protected from the elements. Basically, it is designed for indoor usage.
The weight of the Spool Welding Robot is approximately 1400 kg.